These two very different companies show that offsite construction can bring quality results to both affordable and luxury projects.
- SI Container Builds converts shipping containers into many different building structures, leveraging cost efficiencies to make them affordable for a wide variety of uses.
- EvoDOMUS caters to the high-end market with modular homes customized to the needs of each buyer.
- In both cases, modularization results in a high-quality product.
When SI Container Builds (SICBS) in Buffalo Grove, Ill., was launched in 2018, the company was installing bare containers on the final home site and then finishing them in place. “Our first build was not in [a] warehouse,” says Rory Rubin, Founder and CEO.
However, they have since moved to a warehouse and can now build to scale. To date, SICBS has converted dozens of containers for a variety of uses including backyard accessory dwelling units (ADUs), vacation homes, studios, rentals and guest houses, as well as single- and multifamily units and commercial spaces.

Photo courtesy of SI Container Builds
As a result of the lack of affordable housing, the influx of immigrants and the high numbers of homeless, Chicago is experiencing a massive housing crisis, Rubin says, “There aren’t even [affordable] places to rent. So, the fact that we can build faster, to code and [to a high standard of quality] can really help.”
SICBS is licensed and certified to build in all 50 states. The choice to use the shipping container lends itself to non-profit projects like SheCare Wellness Pods, which offers free mental-health services, educational workshops, and rest pods for silent respite. SICBS is also currently working with the Boris Lawrence Henson Foundation and katespadeny, in a partnership that aims to reach more than 25,000 Black women attending Historically Black Colleges and Universities (HBCUs). In addition, SICBS built a tiny house container village for Petite Retreats — vacation getaways located across the country.

Photo courtesy of SI Container Builds
One Trip Only
SICBS purchases one-trip shipping containers, used only once before reaching their destination. The containers are in close-to-perfect condition and, with proper care, have a longer lifespan than most homes, Rubin says.
Reusing a one-trip container as a building structure minimizes waste, plus it can cost up to 50% less. And a shipping container is built to last more than 25 years through harsh sea voyages.
After repurposing, the quality of the SICBS residential units is certified by NTA, a testing and code-evaluation company that was recently acquired by the International Code Council. It conducts on-site inspections in the 12 states in which the company has done business. The NTA inspections, says Rubin, are “above and beyond what an average builder would be doing.”

Photo courtesy of SI Container Builds
Containers make ideal homes in areas prone to fires, hurricanes and other natural disasters. “A 40-foot container weighs 18,000 pounds, so it’s not moving anywhere,” she says.
The exterior of the container can be left as is except for two coats of marine-grade paint, or it can be clad with various materials to blend in with adjacent structures. Rubin built an office in her backyard that was clad to match her 100-year-old stucco home. “It has the integrity of a steel structure, yet it doesn’t look like one,” she says.
Most clients are businesses, including home builders, foundations and non-profits. “We are talking to developers,” she says. “We’re a perfect fit for infill.”
Standardized Layouts
SICBS standardizes as much of the production process as possible. “We have standardized layouts that people can choose from,” Rubin says. “There are some selections they can make for the interior. This gives people options to customize their homes while keeping things simple.”
The company offers 20-f containers that convert into home offices or studio apartments for backyards. The next size up is a 40-foot container that can be configured with either an end bath, a walkthrough bath, or a hall bath.
Two containers are combined to create a two-bedroom, one-bath unit with a laundry area. The largest model, a combination of three containers, is a three-bedroom, two-bath unit that some buyers have upgraded with a mudroom.
SICBS can complete a build in approximately eight to 12 weeks, depending on unit size. “That’s once we get an order that has been approved for a permit and has architectural plans, which we do in-house,” says Rubin. “We can provide an awful lot of units for people that need them quickly.”
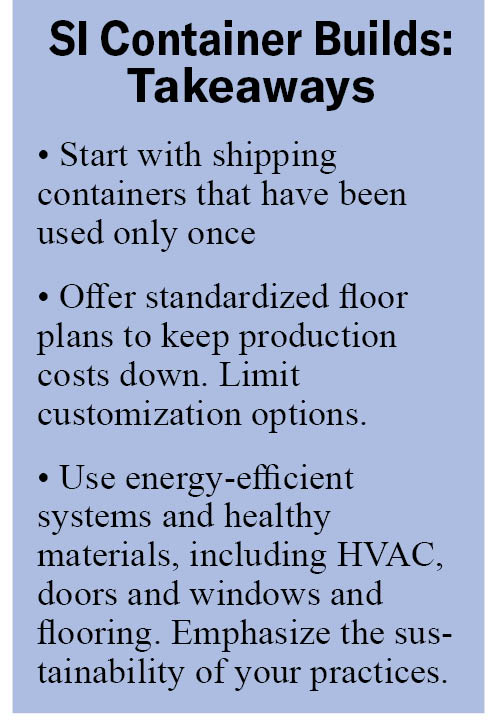
No Two Alike
In contrast, Cleveland, Ohio-based EvoDOMUS provides a true custom-home design and construction experience, only the homes are modular. “We see ourselves as a design and build firm with an emphasis on sustainable home building,” says Co-Founder and CEO Alexander Kolbe, AIA Int’l Associate, RIBA, ALA Allied Professional.
EvoDOMUS builds two to four homes a year, on average, and for a high-end clientele: each home ranges into the millions. Their work is primarily in the northeastern United States. Modules are fabricated by Structural Modular Innovations in Strattanville, Pa.

Photo courtesy of Alexander Kolbe
The company prides itself on starting every design with a hand sketch on a blank piece of paper, “but of course we have the building system in mind,” Kolbe says. “When I talk to clients who are not housing professionals, I explain, ‘Imagine putting a house design through a bread slicer.’ Module width, which is a maximum of 16 ft., is dictated by Department of Transportation regulations for public roads, and we need to slice that design into modules that don’t exceed that width.”
EvoDOMUS encourages clients to put their personality into the project, guided by in-house architects and designers who take site and climate conditions into consideration. The home styles are inspired by Modernism, with clean lines, expanded space and volume, and lots of natural light.
“There is no compromise with modern architecture,” Kolbe says.

Photo courtesy of SI Container Builds
Pushing the Envelope
EvoDOMUS exceeds code requirements in key areas such as insulation, Kolbe says. “For instance, the code calls for R-20, but our exterior walls are R-33 or higher because we want the house to be as [efficient] as possible. Everything we pick for the building envelope is suited for that purpose.”
The company’s MOD+ wall system uses Roxul mineral wool insulation plus a continuous layer of rigid foam insulation to provide R-33 comfort and minimize thermal bridging. The thermal resistance of the roof system is a minimum of R-50, using Roxul mineral wool between the joists plus a minimum of 3-in. rigid insulation above the sheathing.
“We wholeheartedly embrace alternative energy sources such as solar photovoltaics, heat pumps, geothermal technology and other advanced energy systems to supply any remaining requirements or to achieve a net-zero home,” says Kolbe.
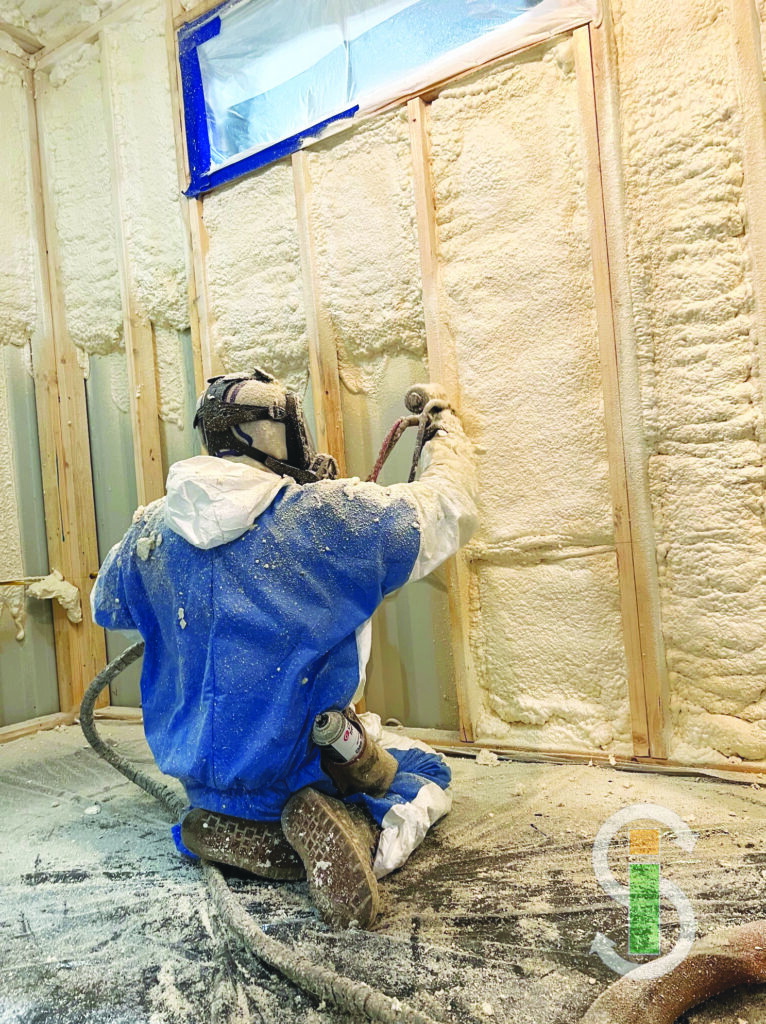
Photo courtesy of SI Container Builds
Passive design methods minimize heat gain. “We optimize windows on the south, east, and west façades, and do solar protection such as sun shading and canopies,” he says.
Occupant health is also important. EvoDOMUS uses low- or no-VOC paints and finishes. Selections include products with high-recycled content, as well as FSC-certified woods and bamboo.
While it’s impossible to avoid change orders entirely, the company minimizes them with a detailed selection process that takes two to three full days. “Clients have to sign off on their selections and plans,” he says.
What sets the company’s homes apart from stick-built is that modular can cut construction time up to 50%, depending on the local contractor doing the on-site work, Kolbe says. Once modules are set, it typically takes approximately four to six months to complete the home.
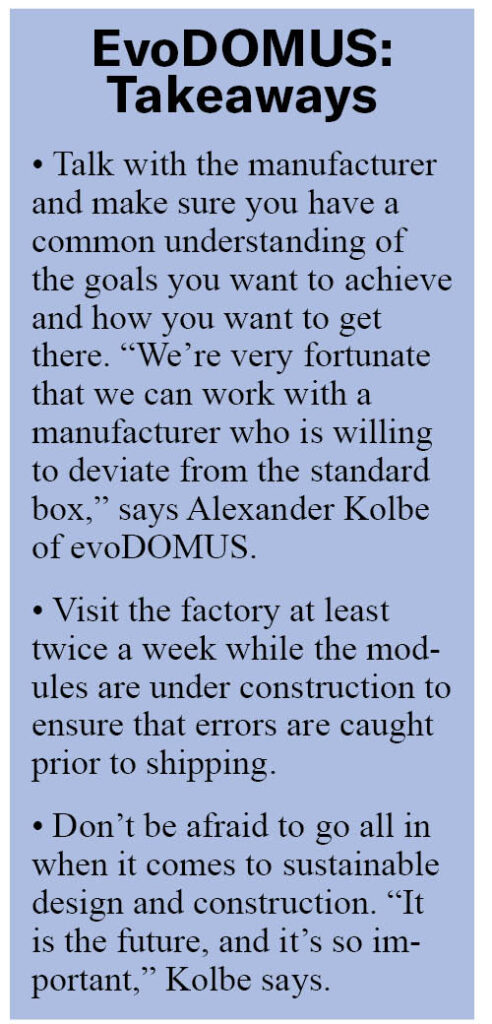
Cost Considerations
Custom modular homes don’t come cheap, and evoDOMUS is no exception. Since the company does not sell plans off the shelf, the cost of the home depends on the size and complexity of the design, the site constraints and the client’s specifications. Finished costs for the home, including planning costs and the local contractor’s charges, typically range from $425 to $550 per square feet.
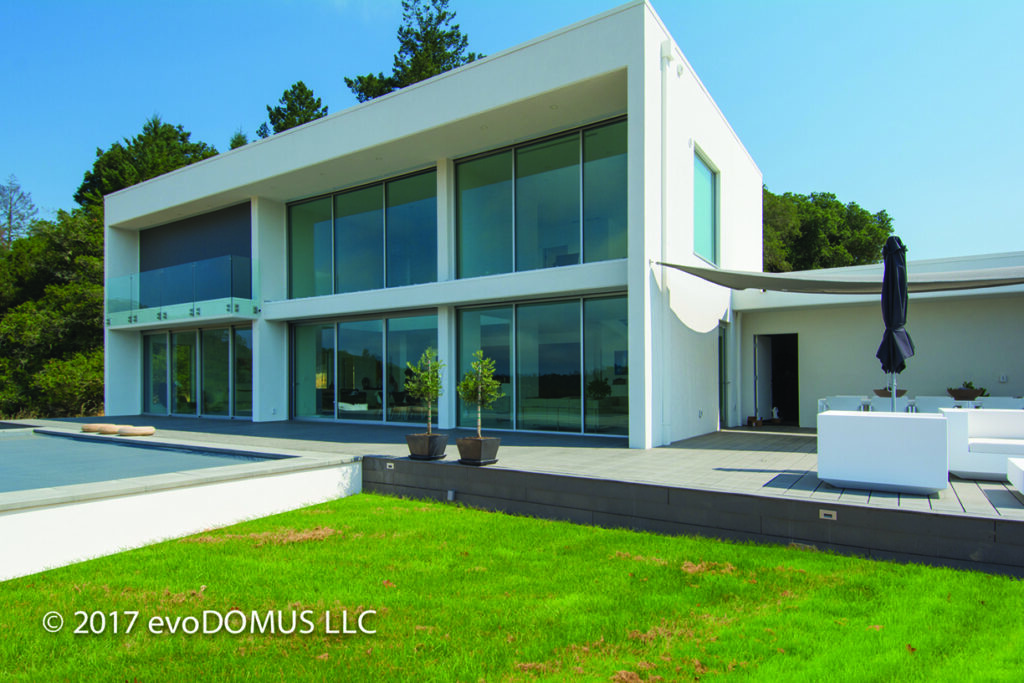
Photo courtesy of Alexander Kolbe
“Having said that, costs for more luxurious designs with extensive amounts of glass, complex structures, or expensive fixtures can be significantly higher,” Kolbe says. Locations with high labor rates such as the Hamptons on Long Island in New York, the Colorado mountains, or islands anywhere, will also push costs higher. “We have seen project budgets north of $700 per square feet in those areas,” he says.
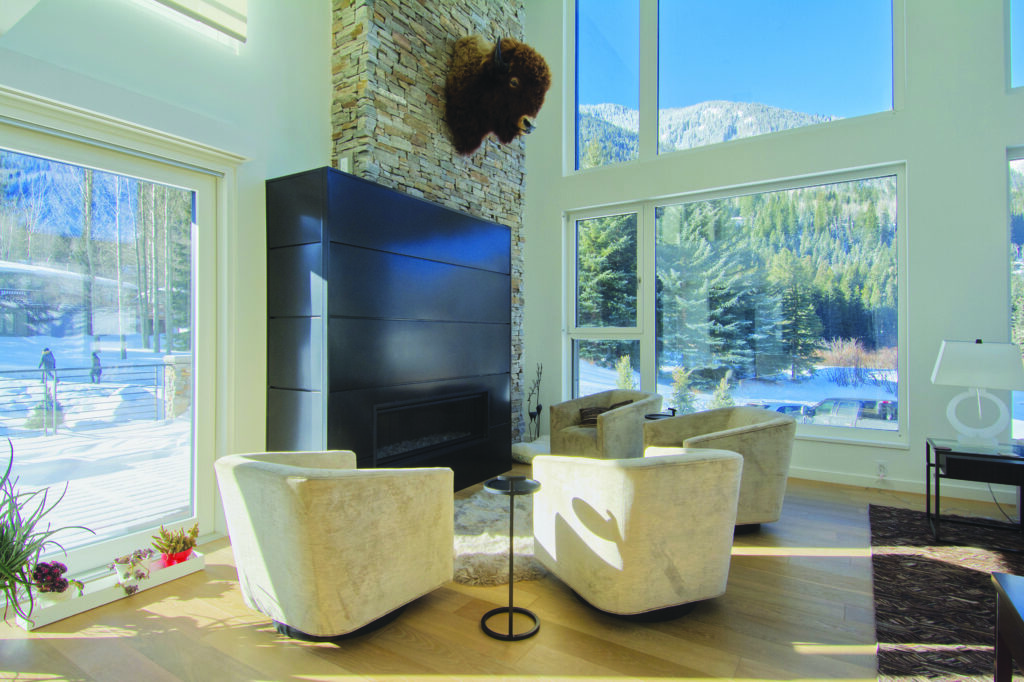
Photo courtesy of Alexander Kolbe
However, evoDOMUS clients, who are knowledgeable and well-versed in sustainable home building, are willing to make the investment. “The first phone call often starts with, ‘I’m so glad I found you. This is exactly what I want.’”
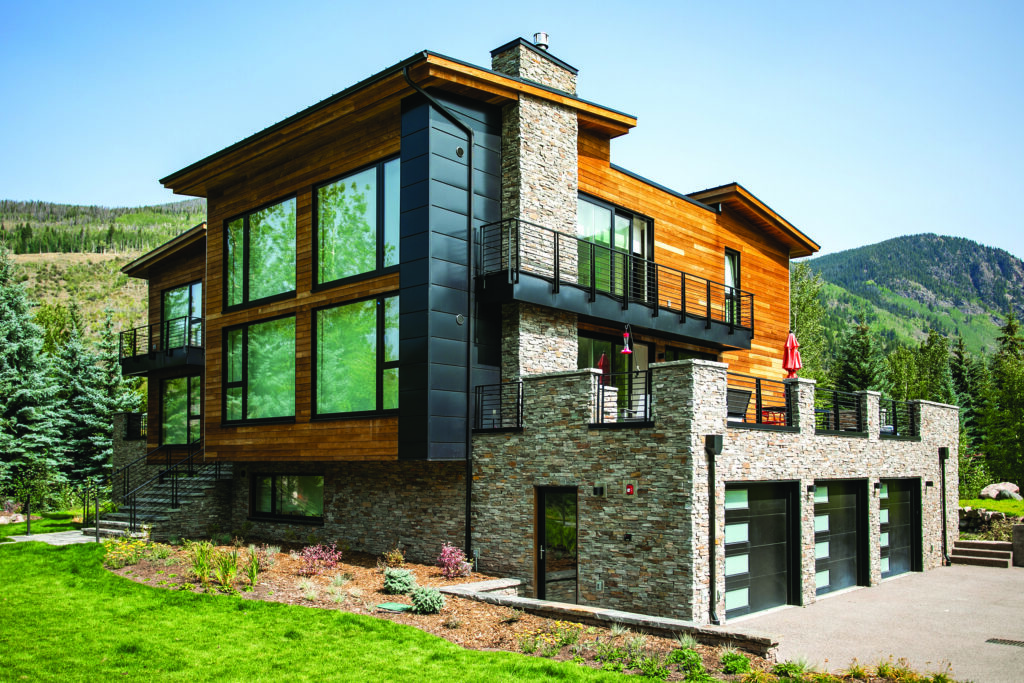
Photo courtesy of Alexander Kolbe
Susan Bady is a freelance writer based in Chicago, Ill., who focuses on residential and commercial design and construction topics including sustainability and building technology.