Making one product at a time will solve problems that many offsite factories don’t know they have.
- Batch production may seem like a good idea, but in reality, it slows production and causes other problems.
- One-piece Flow (OPF) is a best practice in many industries because factory operators know that it saves time, reduces waste and improves quality.
- Although it can be a challenge to implement OPF, the author offers some recommendations that will make the process easier.
In most modular factories I’ve visited and worked in over the years, I’ve observed a common sight: Work in process (WIP) stacked up at various stations, waiting to be installed in a module, pod, or assembly. I’ve seen cripplers, headers, spacers and backers piled up in the mill area or the framing stations, duct sub-assemblies lined up in the HVAC station, even entire walls or floors stacked in the framing area.
This is the result of batch production, or “building ahead.” It can seem to make a lot of sense at times, especially when workers find themselves idle, waiting for the line to move. It keeps people busy and seems like it will save time later. In actuality, however, producing components in batches slows down production and causes a litany of other problems. There’s a better way.
One-piece Flow (OPF), the practice of processing only one piece at a time at each station as it is needed, is a concept that has become a manufacturing best practice, because it raises efficiency and reduces waste. The practice of OPF is rooted in the principles of Lean Manufacturing, which focus on eliminating waste and maximizing value in the production process.
In this article, I’ll discuss the origins of OPF, the advantages of OPF versus batch processing, challenges in implementing OPF and recommendations for applying OPF in a module or component factory.
OPF can be traced back to the Toyota Production System (TPS), which was developed by Taiichi Ohno in the mid-1900s and is now commonly known as Lean Manufacturing. Ohno observed that traditional mass production methods were inefficient and created a lot of waste. He believed that the key to improving efficiency and reducing waste was to focus on one product at a time and to work in small groups to produce it. This concept became known as One-piece Flow and is a foundational component of Lean Manufacturing.
Why it’s better
A big advantage of OPF is that it allows for a more efficient and flexible manufacturing process. In batch processing, products are produced in large quantities and then stored until needed. This can lead to a lot of wasted time and resources, as well as an increase in the risk of defects.
With OPF, products are produced when they’re needed, which eliminates the need for storage and reduces the risk of defects. OPF also allows for a more flexible production process because easy adjustments can be made as needed.
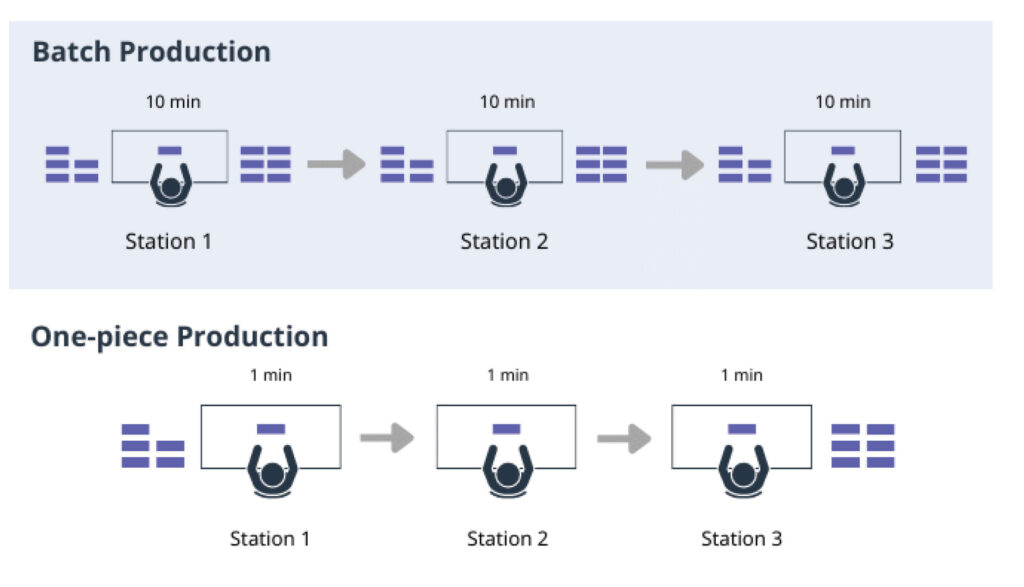
Batch Production Vs One Piece Flow
Another advantage of OPF is that resources get used more efficiently because they are only used when they are needed. OPF also leads to a more efficient use of space, as it eliminates the need for large storage areas.
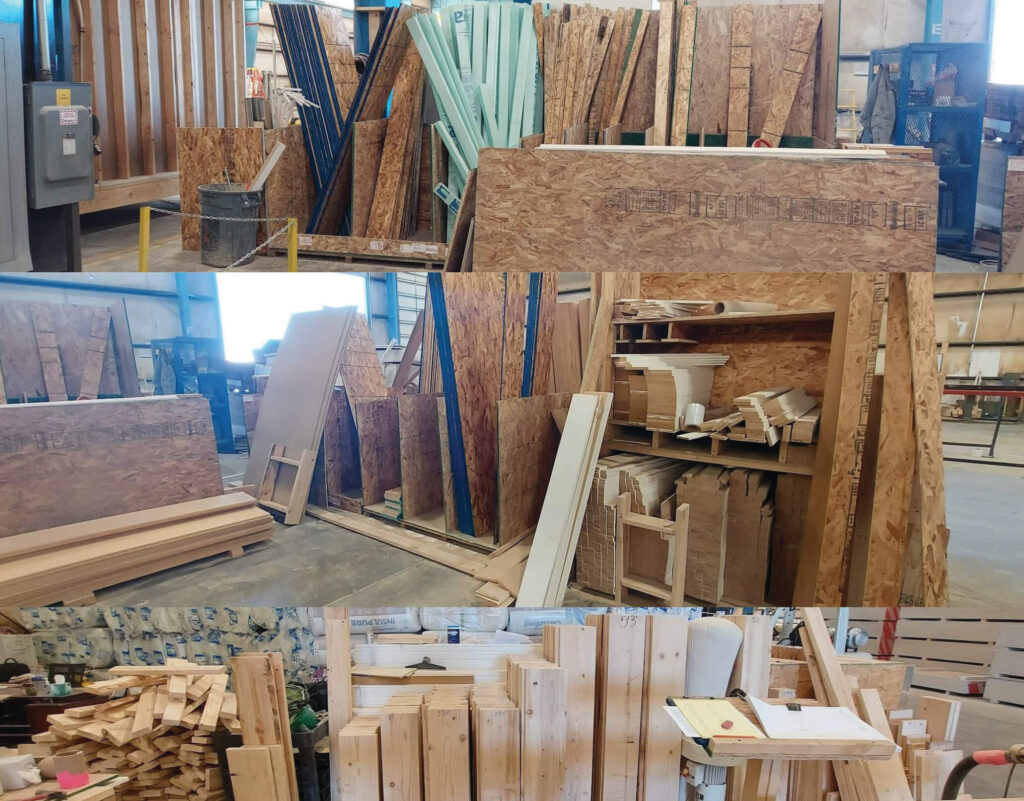
Another benefit of OPF is that it can improve work quality. When products (or WIP) are completed in batches, one-time defects and ongoing production deviations are not detected until the batch is finished. By this time, large quantities of defective pieces may have been produced before inspection and will have to be either reworked or discarded.
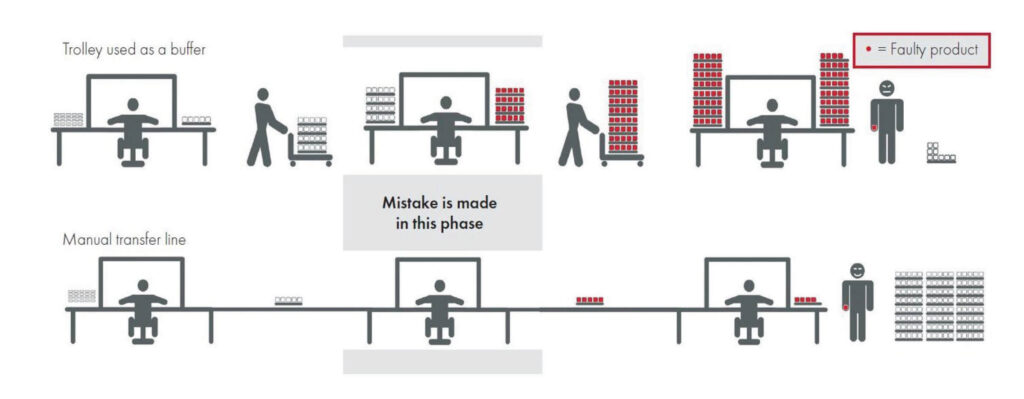
Image source: Treston
Granted, implementing OPF can be challenging, especially in the beginning. It may require a significant change in the production process. And it requires a high level of coordination, precision and accuracy, all of which can be difficult to achieve.
Getting it right
Despite these challenges, here are six recommendations for successfully implementing OPF in your factory.
1. Start small. Begin weaning yourself off building ahead by gradually working down your WIP inventories. This will allow employees to become familiar with the new production process and will minimize disruptions to the existing production process.
2. Implement in stages. Implementing OPF in stages allows for the production process to be adjusted as needed and will minimize disruptions to the existing production process.
3. Provide training. Employees will need help understanding the principles of OPF and how to implement it in the production process. In the beginning, if they have idle waiting time, have them use that time to improve their work process by cleaning, organizing, or looking for waste they can eliminate.
4. Prioritize communication. If you want to succeed, you need to establish clear communication among different departments and employees to ensure that everyone is on the same page and working towards the same goal.
5. Use Kanban. One of the best ways to apply OPF in an offsite construction factory is to use a Kanban, or Pull, system. This is a manufacturing approach where items are produced only when a signal is received that an item is needed, rather than producing items in advance. Train your people to only produce components when they get the signal. (More to come on Kanban in a future article.)
6. Monitor and measure. Finally, it’s important to monitor and measure the performance of the production process to ensure that OPF is being implemented effectively. This can be done by tracking key performance indicators (KPIs) such as production time, defects and resource utilization. This will enable you to identify areas where improvements can be made and to adjust as needed.
Although perhaps counterintuitive, working toward One-piece Flow is a powerful way to further increase your throughput and quality, decrease costs, and balance your labor across your manufacturing line.
It may feel foreign or even risky at first, but it will pay big dividends down the road.
Daniel Small is a Denver-based management consultant to the building industry. He specializes in Lean Construction and Manufacturing and Six Sigma methodologies. Contact him at [email protected]