It will take a wide range of college and private training to drive growth in offsite construction.
- Many colleges are starting to look at offsite, and industry companies want to partner with them. But colleges need to put more focus on the standards that apply to this industry.
- Hands-on installer training will be an essential part of helping existing trades become more comfortable with offsite.
- A sometimes-overlooked way to grow the industry is the sharing of information on offsite methods among contractors, some of whom may be competitors.
Exponential growth in the offsite industry will require more exposure to offsite methods in colleges, as well as organized training solutions from for-profit businesses.
There’s no one-size-fits-all solution. Instead, training approaches will reflect the local market, the sponsoring institution or company, and the priorities of the instructors. Here are a handful of examples:
Teaching IC Theory
A decade ago, late University of Florida Professor Dr. Charles Kibert — an instructor of industrialized construction, value engineering and construction techniques — received a grant from the Department of Labor to create a construction manufacturing course that was later shared with six colleges in the State of Florida.
Now, one of his former students, Dr. Arezou Sadoughi, is an Assistant Professor in the Department of Sustainable Technology and the Built Environment at Appalachian State University and a consultant at her private firm for zero carbon modular design. She credits her late advisor for her current path.
Sadoughi teaches an Industrialized Construction (IC) theory class for undergraduates where they learn about the history of modular construction, project management, DfMA, lean construction manufacturing and the sustainability of manufacturing. As their Capstone project, students practice estimating and scheduling for modular preconstruction.
“The integration of modular design is much more important with industrialized construction,” says Sadoughi. ”Manufacturers cannot obtain the benefits of automation without incorporating integrated autonomous design.”
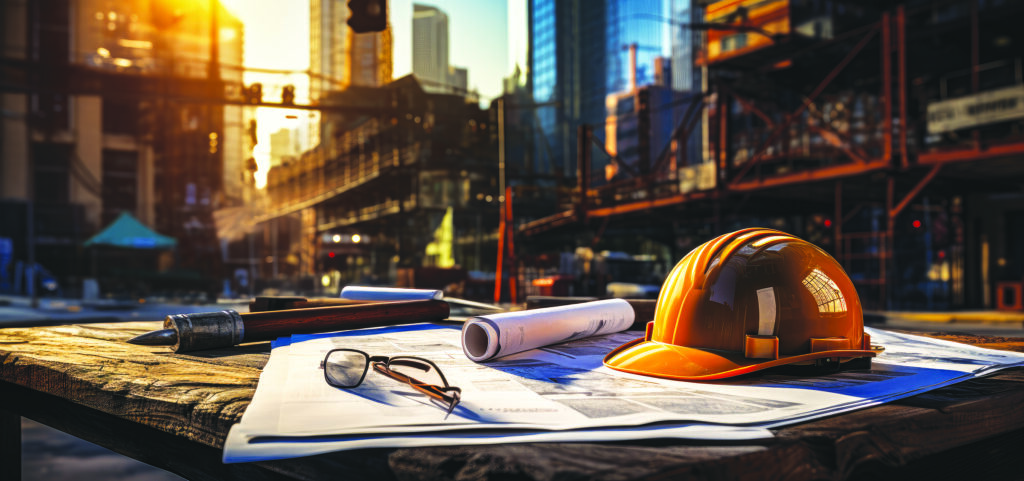
College-Industry Partnerships
Richard Chiavetta, Director of Design for R&S Tavares Associates, a modular design and engineering firm based in San Diego, Calif., believes having a baseline knowledge of industry standards could help push modular design and assist in the learning curve for students unfamiliar with modular methods.
Unfortunately, he says that this basic introductory knowledge is not being taught at most colleges. “It’s at least six months before we’re able to take the training wheels off [of new hires],” says Chiavetta. “Nine months for engineering. There’s a huge learning curve that gets applied.”
Tavares Associates does much of its engineer and architect recruitment from University of California San Diego (UCSD) and The New School of Architecture, Chiavetta’s alma mater, and where he first met Pedro Tavares in a graduate program studio class. He says that if either school would adopt an introductory course around industrialized offsite construction, their group would be happy to offer internship programs.
The University of Denver’s Franklin L. Burns School of Real Estate and Construction Management offers a relatively new Offsite Construction 101 class, taught by Professor Eric Holt and built in collaboration with MiTek. Professor Holt regularly interacts with the NAHB Student Chapter Advisory Board and recently surveyed the faculty to better understand their knowledge of offsite construction. Not surprisingly, he found a lot of confusion around terminology.
“One of the biggest challenges with academia is to get us all on the same page with terminology,” says Professor Holt. “So, when someone says ‘manufactured housing’ or ‘modular homes’ or ‘offsite construction’, we all know what we’re talking about.”
Purdue University, Clemson University, North Dakota State University, California State Polytechnic University, and Brigham Young University are also exploring the use of the curriculum in their construction programming. Currently, Professor Holt uses the lesson in his Construction Building Systems Class that includes a factory tour. Offsite construction is also mentioned as an option for vertical construction in the school’s Residential Development class.
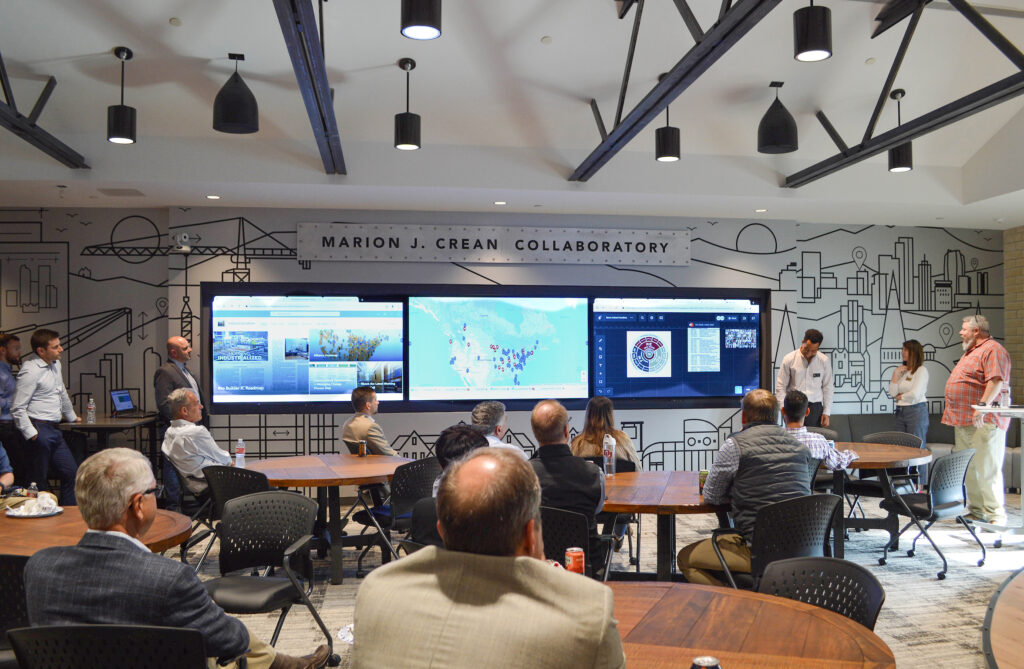
Photo courtesy of: Ceci Smith – The Burns School
Hands-on Training
Crane operator licenses did not exist when Roger Lamoreux began his career. He was the ninth person to receive a crane operator’s license in the state of New Mexico and has now run his own business, Lamoreux Crane Service in Santa Fe, for 43 years.
Lamoreux is a frequent contributor at installer training events hosted by B.Public Prefab, a high-performance panelized manufacturer that’s also based in Santa Fe. He shares his thoughts around safety with attendees, interacting with them as they learn and practice crane signaling. “You can replace a building, but not a life,” he says.
The certification process to operate a crane can be lengthy. As an example, the state of New Mexico Hoisting program requires a NCCCO (National Commission for the Certification of Crane Operators) or other nationally accredited license prior to applying for a state license. 500 hours of seat time is then required under a licensed/certified crane operator on the specific crane type you are trying to obtain certification for. This process can take anywhere between four to eight months, depending on the type of crane and training program.
“There’s a different certification for each type of crane,” says Lamoreux. “The higher the weight means having to become certified in that range.”
Candidates must be at least 18 years of age, have a valid CDL and medical card, complete a nationally recognized training course and certification, pass written and practical exams that demonstrate knowledge/skill, undergo a pre-employment physical exam, and understand relevant safety regulations and industry standards.
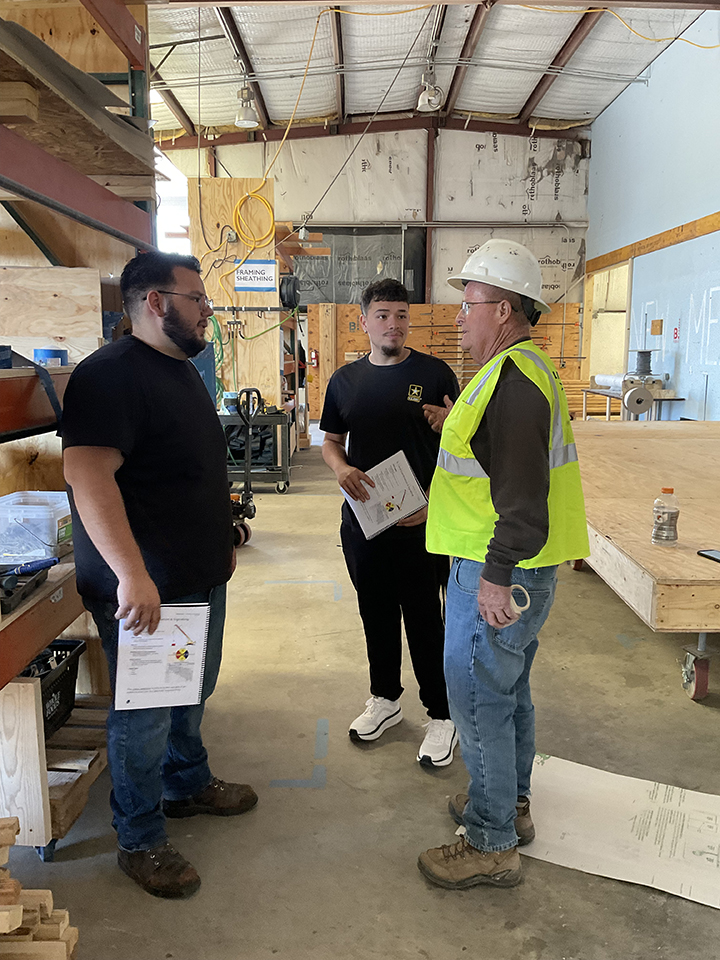
Photo courtesy of: B.Public Prefab
Contractors Sharing Knowledge
Brown Construction in Sacramento, Calif. is a 60-year-old, employee-owned general contracting company focused on projects throughout the state. Although they’ve been successful as an on-site general contractor, Assistant Preconstruction Manager, Michael Wlosek, has been exploring how to effectively and efficiently begin working with the offsite industry.
A decade ago, Brown bid on their first modular project. Although they couldn’t participate due to timing, they are being asked more frequently by developers if they can assist with modular projects.
“Everybody is looking for ways to make projects pencil,” says Wlosek. “We typically get approached by developers who have entitlements or own land and want to do something with it.”
With only what he would call “cursory knowledge” of offsite, Wlosek began his deep dive into general contracting for modular at the World of Modular conference in March of this year. He found, in general, that modular is a very “inwardly focused industry” and there is a lack of information on how to participate as a modular GC.
Wlosek has been proactive in reaching out to factories and experienced modular GCs to learn the ins and outs of the offsite side of the industry and credits Colby Swanson (an experienced construction technologist and innovation strategist) and modular construction manager CJ Myrick for talking with him at length about the industry.
Volumetric Building Companies in Tracy, Calif. provided a tour of their manufacturing facility, and Kirk Hall of Accuset, a modular installation company based in Washougal, Wash., also invited him to see their projects and learn about different installation methods.
“The knowledge exchange in this industry is massive. Not only did Kirk pick up the phone at 5pm on a Tuesday, but we were on-site the next morning. He gave us three hours of his time walking us through the entire project from top to bottom.”
Nibby Prefab, a division of Nibbi Brothers General Contractors in San Francisco, Calif. — a union shop and potential competitor to Brown — also took time to explain the pitfalls to avoid and the ins and outs of estimating. Nibby believes information sharing is essential to elevating the whole industry.
While Wlosek has done his homework, he’d love to see more GCs, developers and subcontractors invited to attend open houses and walk projects to increase their involvement with stakeholders. Wlosek realized how invaluable it was to walk the projects with Accuset and to get immediate answers to scope, sequencing, scheduling and tolerance questions.
“It seems like the weak link in the modular industry is the general contractor,” says Wlosek. “If a modular project goes bad, the modular industry becomes the scapegoat whether or not it was the fault of the GC. The right GC needs to be an educated GC.”
How is your company working with schools and stakeholders to create training and development programs that benefit the offsite industry? Get in touch and let us know.
Heather Wallace is the Communications Director at Momentum Innovation Group, a consulting firm that is working with the modular industry and educational institutions to develop a curriculum that will help drive more students to the offsite industry.