Employee training is crucial to getting the most from a Lean program
“No goal, regardless of how small, can be achieved without adequate training.” – Taiichi Ohno
Employees’ Role in Lean
Research consistently demonstrates that engaged and skilled employees are the driving force behind every successful Lean manufacturing operation. When employees are equipped with all of the necessary knowledge and skills for their jobs, they become invaluable assets to the factory.
Empowered employees are an invaluable asset. They contribute to improved productivity, quality and operational efficiency. They actively participate in problem-solving, process improvement and waste reduction efforts. They have a positive impact on the overall performance of the factory.
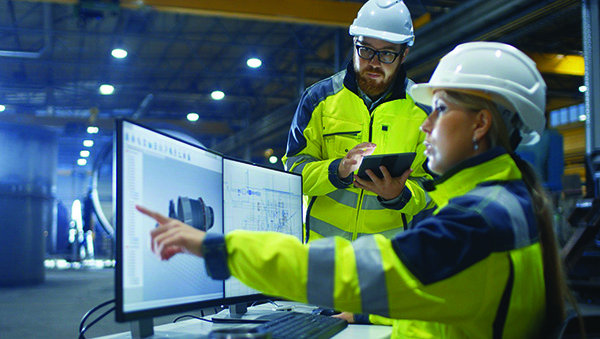
What Training Do You Need?
To ensure that your training programs are properly targeted, you should start by conducting assessments to identify specific skill gaps in your workforce. These assessments may involve skills gap analyses, performance appraisals and/or employee surveys.
The effort put into discovering and understanding the areas that require improvement is a crucial first step. You will be able to design training initiatives that specifically address the needs uncovered by the assessments. This approach will maximize the impact of your training programs and will help you to focus your investment in skill development.
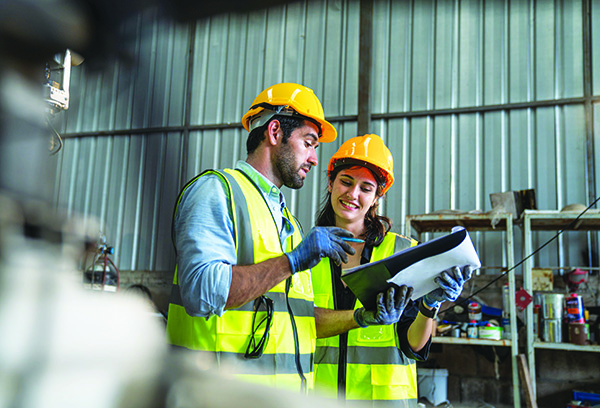
An Effective Training Program
The effectiveness of a training program is dependent on how well it’s designed and delivered. In particular, interactive and experiential learning methods are among the most effective. They have proven to be highly successful in enhancing knowledge retention and application among employees.
Interactive and experiential training can incorporate a variety of training techniques. These include hands-on simulations/practice, role plays, real-world case studies and workshops. The goal is to engage employees actively, and to encourage them to apply their newly acquired knowledge in practical scenarios. By creating engaging and immersive training experiences, you also help to foster a culture of continuous learning and improvement within your workforce.
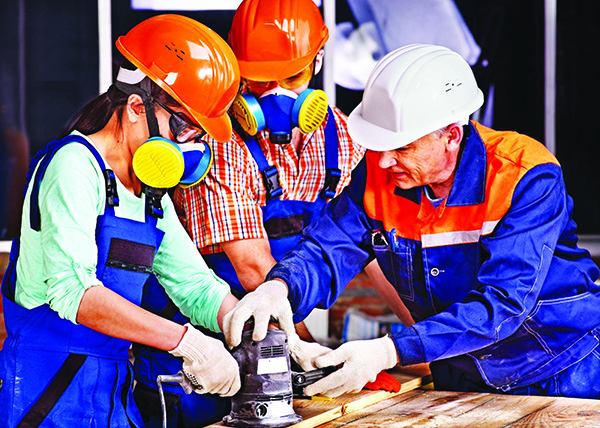
Technical and Operational Training
Technical proficiency is critical to Lean manufacturing. Employees need to have the necessary technical skills to operate machinery, build code-compliant building components and adhere to safety protocols. By providing comprehensive technical training, you can equip your employees with the expertise they need to perform these tasks efficiently and safely.
Cross training is also important. The cross training of employees in multiple trades/subprocesses will make them more versatile, which will help insulate your company from labor shortages, absenteeism and volume fluctuations.
Another benefit of training is improved safety. A well-trained workforce not only improves operational efficiency, but also minimizes the risk of accidents and errors, thereby enhancing your overall productivity and quality.
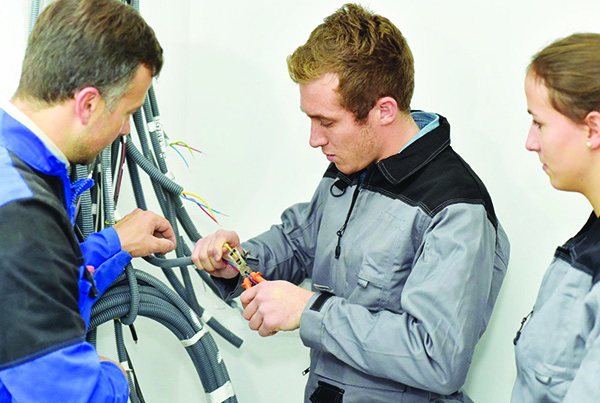
Principles and Methodologies Training
While technical training is crucial, it’s not the whole picture. If you want to establish a culture of continuous improvement within your factory/shop, you also must introduce employees to Lean principles and methodologies.
You should train employees in Lean tools and techniques such as the 9 Offsite Wastes, 5S workspace organization, Kaizen, Value Stream Mapping (VSM) and standardized work. This provides your workforce with the knowledge and tools they need to identify and eliminate waste, streamline processes and optimize resource utilization.
These Lean practices drive efficiency and productivity gains. They improve customer satisfaction and give your company a competitive edge in the market.
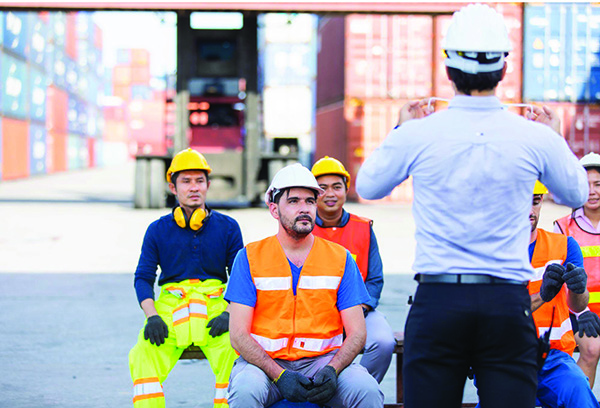
Don’t Forget Leadership and Soft Skills
While the development of technical expertise and Lean skills are crucial, it’s also important to develop your employees’ leadership and soft skills.
These skills include effective communication, problem-solving abilities and teamwork, and they’re vital components of Lean manufacturing success. Investing in leadership and soft skills training fosters a collaborative and cohesive work environment. Improved communication channels, enhanced problem-solving capabilities and stronger team dynamics contribute to higher employee engagement and satisfaction.
Moreover, these skills empower employees to take ownership of their work, to make informed decisions and to contribute more effectively to the factory’s continuous improvement initiatives.
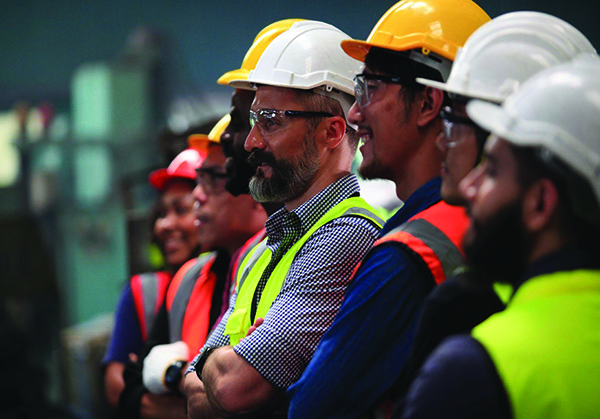
How Effective Is Your Training Program?
To ensure that training programs deliver the desired outcomes, it’s important to establish mechanisms to evaluate their effectiveness. Collecting and analyzing key performance indicators (KPIs) is essential in assessing the impact of training initiatives.
KPIs may include productivity metrics, quality measures, waste reduction data and employee feedback. Post-training surveys, focus groups and performance reviews provide valuable insights into the effectiveness of the training programs and help identify areas for improvement. Regular evaluation ensures that training efforts remain aligned with your goals and enables continuous refinement of your training initiatives.
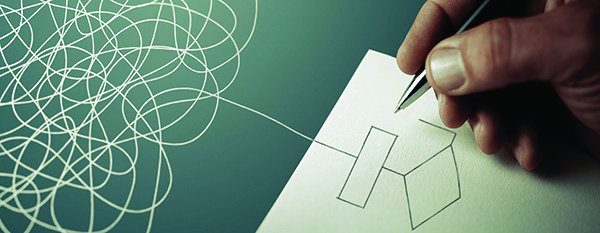
It’s About Unlocking Potential
Employee training and skill development serve as catalysts for unlocking the true potential of a Lean manufacturing operation. By prioritizing the development of your workforce, you position yourself for sustainable growth and success in this highly competitive industry.
If your training programs are properly targeted, your employees will become equipped with the knowledge and skills they need to drive operational excellence, to promote continuous improvement in all parts of the operation and to better meet customer expectations. Embracing the power of employee training in Lean manufacturing is a strategic investment that pays dividends in enhanced productivity, quality and overall performance.
So, get your train on and start reaping the rewards.
Daniel Small is a Denver, Colo.-based management consultant to the offsite construction industry. He specializes in Lean Construction and Manufacturing and Six Sigma methodologies. For assistance with improving your offsite manufacturing process, contact him at 719-321-1953 or [email protected]. Or visit www.LeanOffsite.com.