Impresa Charlotte’s 8,200 square foot, 14-module home illustrates the architectural versatility of modular construction.
- The project was complex and included a lot of site detailing. However, the build time was still half of what it would have been for a full site build.
- The builder worked with the factory to ensure that details were included in the modules to make the home energy efficient.
- The only hiccup was that some of the smaller panelized elements were stacked out of order by the manufacturer. The builder says he will work with the manufacturer more closely on this issue in the future.
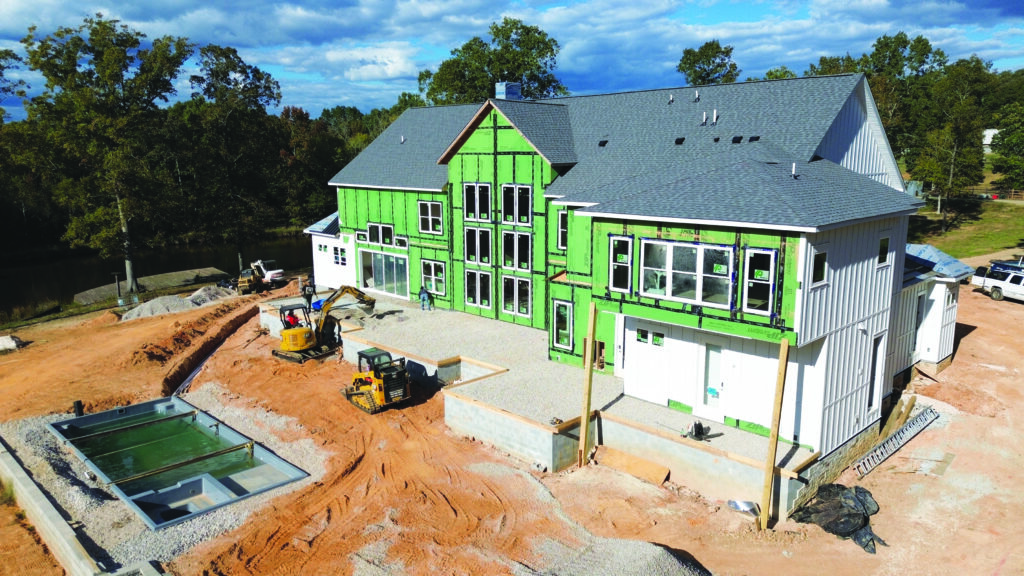
The clients were well prepared with a full set of floor plans in hand when they approached Fernando Calderon to build their new home. “They had spent a lot of time with an architect in order to make sure the house plan offered positive space, energy and balance,” says Calderon, franchise owner and President of Impresa Modular of Charlotte, N.C.
The couple researched modular construction thoroughly before approaching Calderon. He says they weren’t afraid of taking a chance on modular.
“What scared them was the time it would have taken to site build the house, and obviously the cost of the project,” he says. “They asked, ‘Can we replicate this with modular?’ Except for some slight changes, we were able to do it exactly.”
Styled as a modern farmhouse with an industrial feel, the home is set on a 20-acre lot in rural Waxhaw, N.C. The exterior is reflective of the style with its white, vertical board-and-batten siding and stone accents at the bottom. Architectural shingles cover the main portion of the roof, with the lower portions made of metal.
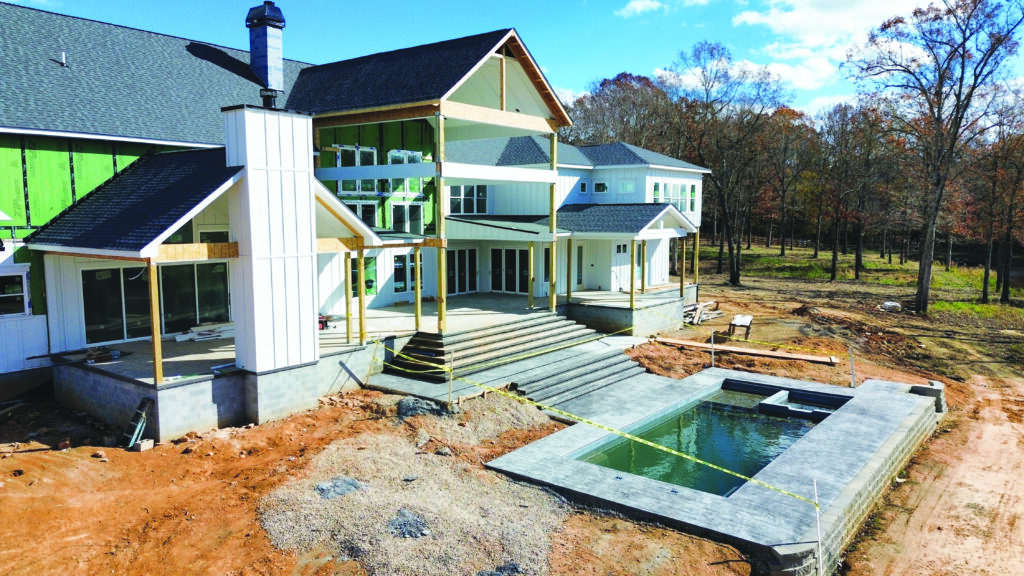
The homeowner notes that the original design represented Industrial Farmhouse while crossing the lines of a barndominium.
“Sometimes barndominiums can feel like they have wasted space because the ceilings are so high,” she explains. “With this home, we were able to get the high ceiling we desired in the great room, though we did concede to 9½-foot ceilings on the first floor instead of 10 feet.”
With 14- and 16-year-old teenagers living at home, and with future needs being top of mind, the clients view the new residence as their family estate or multigenerational home, says Calderon. Five bedrooms may not seem like many for an 8,200 sq. ft. home, but each bedroom is a suite with a full bath.
Besides the primary master bedroom for the clients and a bedroom each for the teens, there is a fourth bedroom that has been designed as a “miniature apartment” to serve multiple uses. “There’s a scullery behind the kitchen with its own refrigerator, range and sink, creating an in-law or extended guest suite,” says Calderon. The fifth and final bedroom, on the second floor, is designated as a guest suite.
The two-story home has an elevator to ensure that family members have full access to living areas should they develop mobility issues.
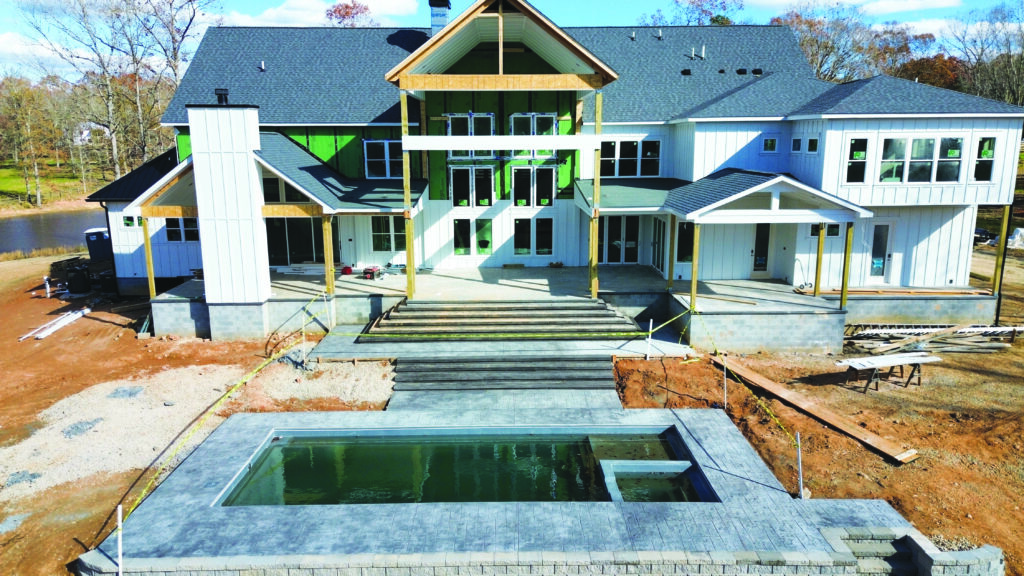
Naturally Sustainable
Calderon is a licensed general contractor in North and South Carolina. He is also a PMP and LEED AP, and an accredited Green Rater. A preliminary HERS rating for the home came in at 56, making it 44% more energy efficient than the average American home.
Factory fabrication ensures that the modular home has a tight envelope, providing greater energy efficiency and therefore, energy savings. “We also did an upgrade that we don’t necessarily do in most of our houses: we used ZIP System insulated roof panels for the sheathing to provide an additional layer of insulation.”
One concern the clients had was electromagnetic frequency (EMF) contamination. “There were specific areas where they didn’t want the thicker cables for the HVAC units to run underneath the living quarters, so we moved them underneath hallways, bathrooms, and closets,” Calderon says.
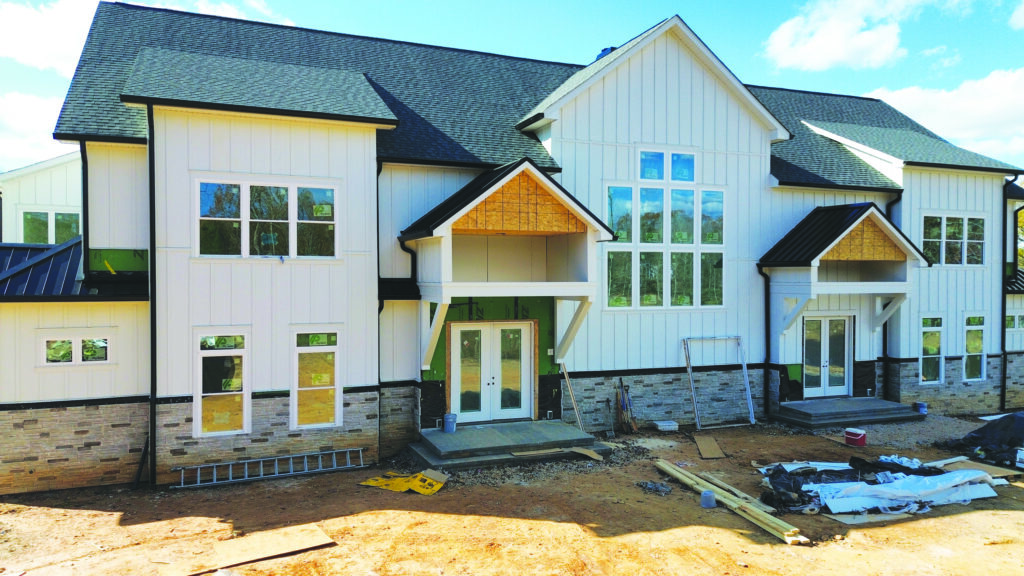
Think Big, Save Money
The home has an open plan on the first floor with large windows that draw copious amounts of natural light, Calderon says. “It feels larger than 8,200 sq. ft. because of the second-floor areas that are open to below,” he says.
The great room is 40 ft. by 20 ft. with a 34-ft. ceiling, evoking the Industrial Farmhouse feel with a high ceiling in the center of the house.
Because of the size and detailing of the home, the design adaptation by Impresa took six months, but in the end the actual changes turned out to be minimal, says Calderon.
“The clients came with a potentially very complicated floor plan that was Feng Shui certified,” he says. “Getting it done with minimal changes was amazing.”
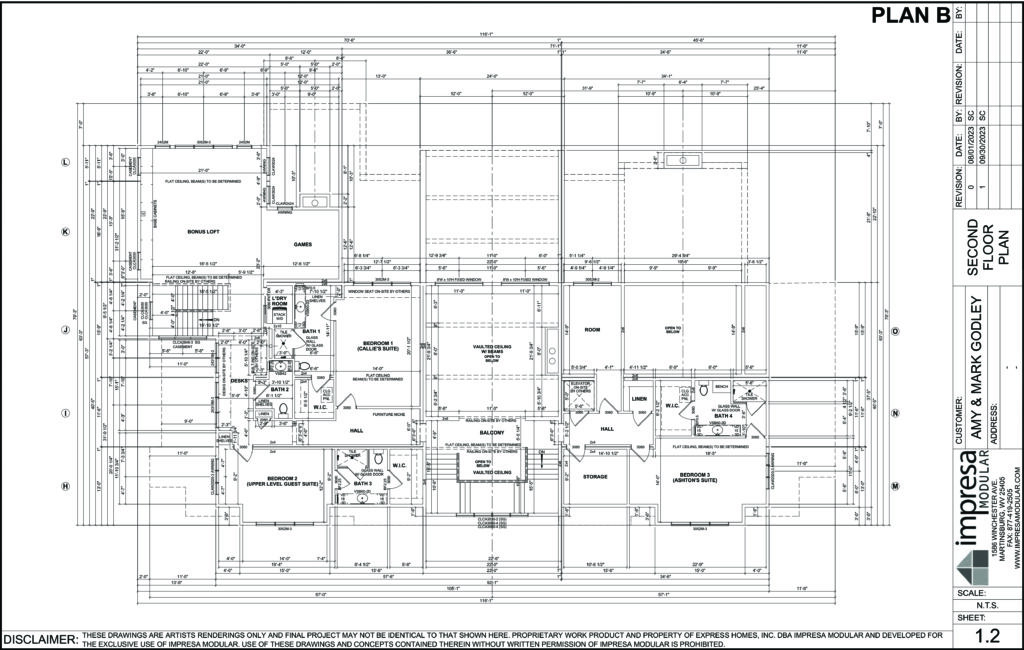
Logistics Challenges
Fabrication and delivery of the modules was done by ICON Legacy Custom Modular Homes in Selinsgrove, Pa. Fourteen boxes were delivered on 17 carriers, with an additional three carriers for parts.
Modules were fabricated in batches of eight per week. Factoring in a pause when crews were working on other projects, the net fabrication time was about three weeks.
One issue that slowed down on-site activity concerned the stacking of parts on the carriers. They had been arranged so that they would remain stable during transit, according to size and weight rather than being arranged in the sequence in which they would be set.
“There were close to 30 roof panels,” says Calderon. “We would set number one, number two, and number three, but number four would be at the bottom of the second carrier and we couldn’t get to it.”
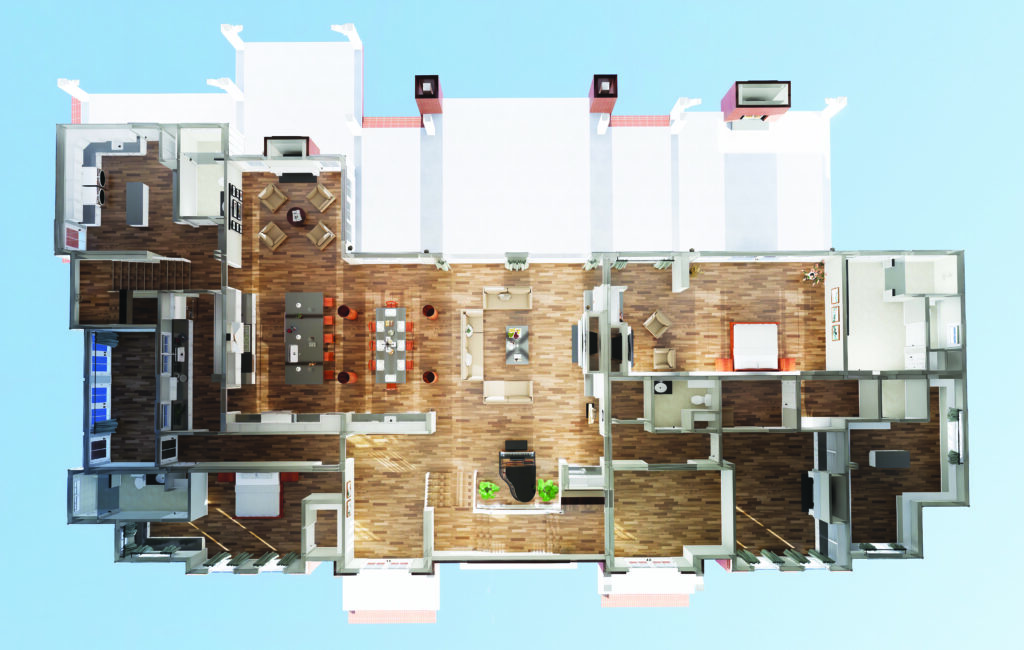
This, he says, shines a light on larger, more complex projects that ship loose parts: “You need to work with the manufacturer to develop better logistics for the packing of carriers to make sure it’s done according to the order in which they’re going to be installed, rather than the way they’re assembled for transit.”
A spell of rainy weather also slowed down installation. “We would get in a day of work, then would have to cut it short and cover the house for two or three days.”
Calderon originally anticipated six to eight full days to set the modules, but, in the end, it required 15. “What took the longest to install were the smaller pieces, such as the panels for the roof sections and a bump-out that was also panelized,” he says.
The effect of those extra few days was minimal; Calderon says that modular construction shaved completion time from 14 to 18 months to six to seven months. He says that the turnkey cost for a modular home of this scope is typically $250 to $300-plus per sq. ft., depending on customization.
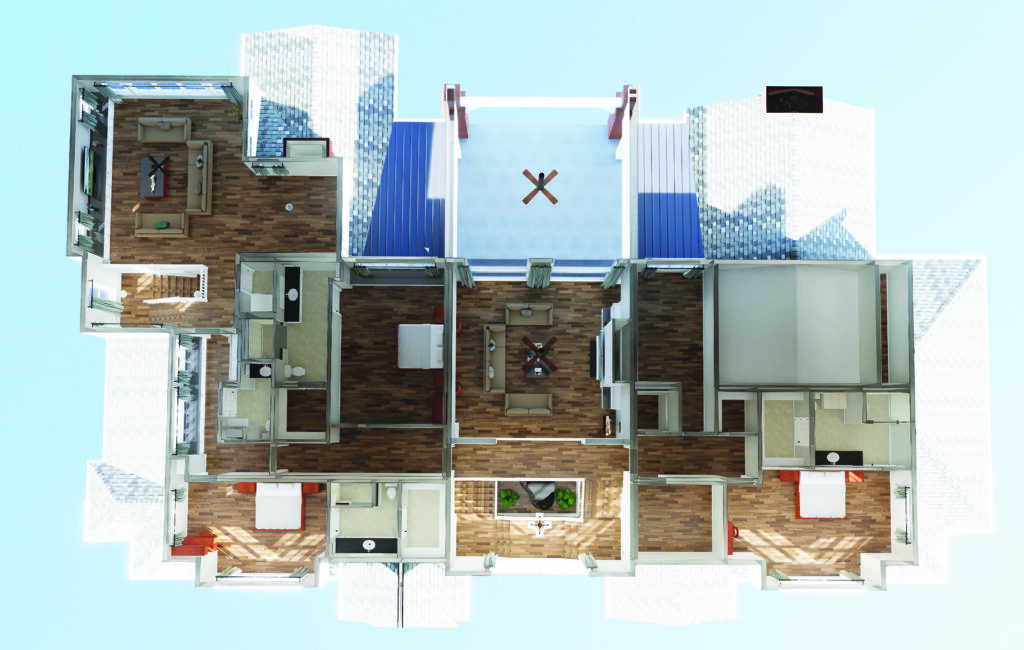
High Ceiling Impact
The feature that people “go wild over” is the 34-ft. ceiling in the great room. “The dimensions of that space make it attractive, but it’s also incredible to realize that it was achieved with modular construction,” Calderon says. “For a house of this caliber, the clients saved a large amount of money and time, and, in the end, the quality is the same as what a site builder could have done.”
He gives credit to the clients for being forward thinking and innovative. “They could have been much more particular,” says Calderon. “They knew it was a challenge and that their home would be one of the few modular homes in the area, but they dealt with it.”
According to the client, “it was important from the beginning that the home match the land and the land match the home. I think we’re blessed and fortunate to be able to build our home on this land surrounded by nature.”
“Modular construction needs to remain an option for consumers,” she adds. “I believe it’s going to become more prevalent going forward because people want a quality product without compromise, not to mention the savings in time and construction costs while having some custom appointments.”
Susan Bady is a freelance writer based in Chicago, Ill., who focuses on residential and commercial design and construction topics including sustainability and building technology. All photos courtesy of Impresa Modular Charlotte.