Before you can improve a process, you have to measure it. Here’s how.
“When performance is measured, performance improves. When performance is measured and reported, the rate of improvement accelerates.” – Thomas S. Monson, President, The Church of Jesus Christ of Latter-day Saints
This is the second in my series of articles on the process optimization framework known as DMAIC—Design, Measure, Analyze, Improve and Control. While you can use this five-step method to get more out of any business process, in these articles I’m applying the principles specifically to the challenges faced by offsite manufacturers.
You’re only going to be able to really improve a process if you understand it deeply. That’s Step 2 of the DMAIC framework.
The only way to fully understand a process is to measure it. Once you’ve completed the Define step and have developed a Project Charter to guide your process improvement (see my article in the July 2022 issue of Offsite Builder), your next task is to measure the current process and to establish a system for ongoing measurement and reporting.
Current State
Identifying weaknesses in a process requires that you take an objective and honest look at the current state of the process, no matter how painful it may be to do so. Only in this way can you determine what’s broken (or at least what’s suboptimal) and begin the process of fixing it.
It may be tempting to go easy on yourself by only measuring the strengths of the process, by not digging too deeply, or by sugarcoating the results. Don’t do it. Suboptimal processes are a sickness to your business and to cure that sickness you have to take your medicine.
Your initial measurements not only will help you identify where to start with your improvement efforts, but they will also become your comparison baseline for future, post-improvement measurements to help you track your progress.
Baseline Metrics
One of the major objectives of the Measure step is to produce baseline metrics for your process. How is the process performing now and what measure will you use to compare current performance to post-improvement performance?
For example, you could measure things like current cycle times, labor hours, Process Cycle Efficiency, defects and more. Each of these measurements can be performed on a completed production unit basis (a module, a panel, 100 subassemblies, etc.) to provide an overall baseline.
In addition, you can, and should, also apply these measurements to each sub-process—framing, wall assembly, MEP rough install, drywall hanging, finishing, sanding, painting, and so on. These sub-process measurements will help you identify the weaknesses of each process and establish baselines, in terms of time, cost, quality and safety.
Data Collection Systems
How do you get started with data collection? One way is to use manual data collection systems such as paper travelers, logs, or quality control sheets, in combination with a spreadsheet recording system. A lot of factories do this.
If you opt for a manual system, it’s important that employees have a data collection template. The template should prompt them to collect data at appropriate times and record any information about the data collection event, including the person collecting the data, the process involved and the environmental conditions.
However, manual systems aren’t ideal. While they’re better than nothing in the near term, they are labor-intensive and subject to omissions, inaccuracies and variation. You should make it your goal to migrate to a digital solution as soon as possible.
Using a digital or software-based system such as Moducore, Manufacton, or Offsight, will allow you to collect, analyze and visualize data automatically and in real-time. Though these tools require a non-trivial investment to purchase/subscribe to and set them up, they will dramatically increase the accuracy, comprehension, resolution and usefulness of your data. These systems will also save you massive time in data collection, manipulation and analysis.
Digital forms like this one provide a fast, paperless and real-time way to collect detailed data on processes such as QA/QC inspections.
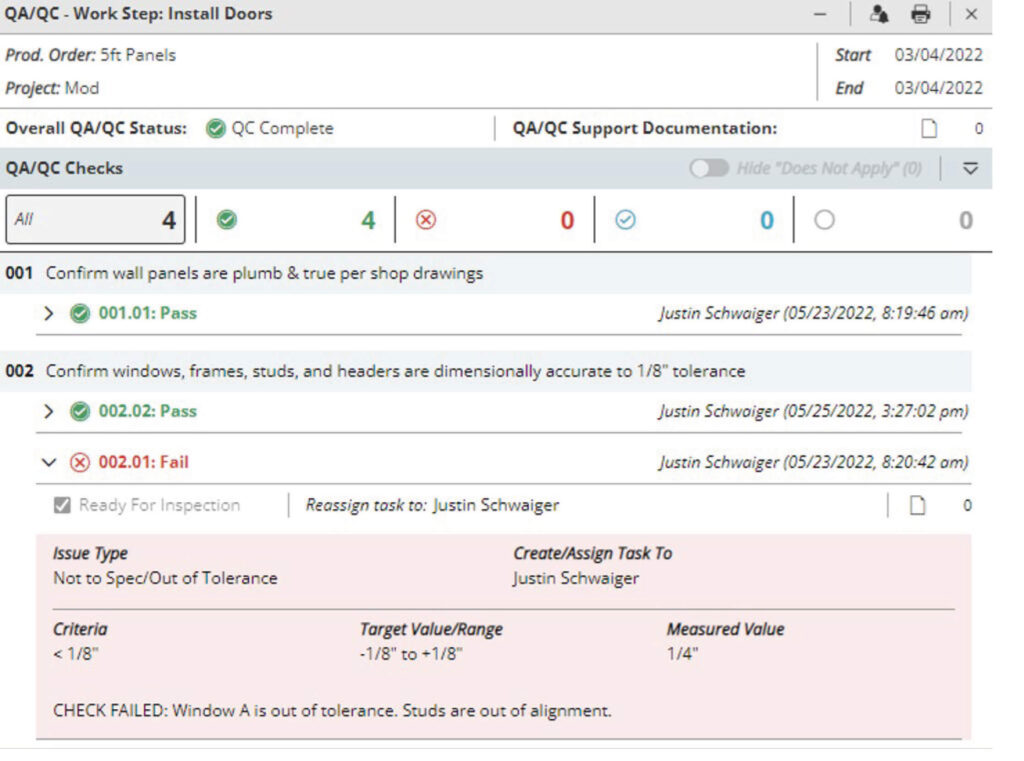
At the quantities being produced in an offsite construction factory, you should try to measure data for the entire population of output — every module or assembly you manufacture — as opposed to measuring data for random samples only. Population-level data is much more accurate than sample-level data and digital data measurement systems make collecting and reporting it easy and accurate.
Reporting
Once the baseline metric or metrics have been established, performance should be reported to all process workers and leaders on a frequent, ongoing basis, preferably graphically and in real-time.
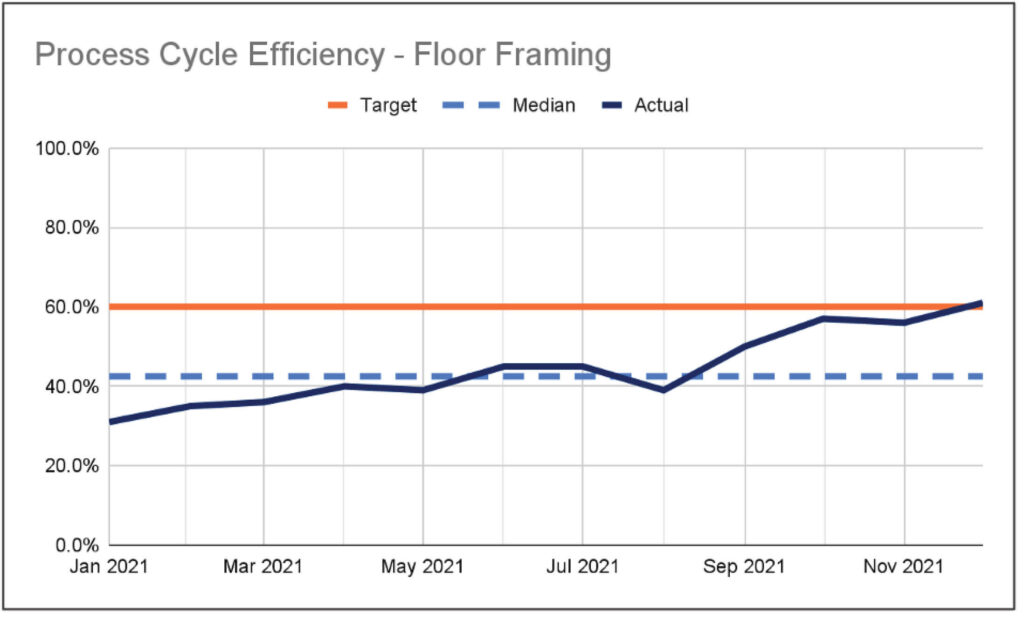
A very effective method of reporting is to print out blank charts at the beginning of a reporting period and to have workers fill in the data on their areas of responsibility by hand at the end of each shift. For example, they could write in their daily numbers on production, safety, errors and more. This guarantees full visibility and understanding of the data and provides an opportunity for real-time feedback, both celebratory and constructive.
Often, providing workers with this type of real-time, clearly-relevant data, along with incentives for KPI target achievement, will prompt a noticeable improvement in results in directly controllable metrics such as safety or attendance. Knowing where things are in a process, and how they are getting better, gives workers real motivation to improve further.
For more complex or opaque metrics, such as Defects Per Module or Process Cycle Efficiency, the data will need to be analyzed further to discover the root causes of issues and identify effective solutions. That’s where the Analyze step comes in, which will be the subject of my next article. Stay tuned.
Daniel Small is a Denver-based management consultant to the building industry. He specializes in Lean Construction and Manufacturing and Six Sigma methodologies. Contact him at [email protected]