The author traveled the US, visiting prefab housing plants coast to coast. Here are his impressions.
- While few modular plants can afford automation, they are nevertheless highly efficient and quality-conscious, and their employees seem satisfied with the work.
- About half of the factories visited were open-minded about experimenting with new processes that could improve quality or efficiency. However, implementation tends to be somewhat slow.
- Everyone is struggling with the need to meet ever-stricter energy codes. In fact, this need has been a factor in factories’ willingness to try different ways of doing things.
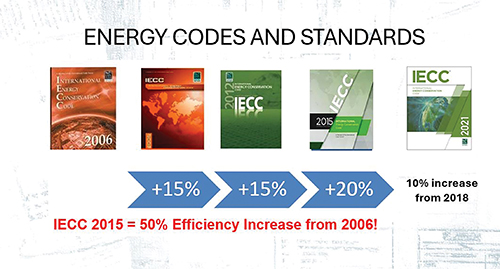
In January of 2024, I started a new role at Rmax, one which focuses specifically on the offsite construction market. To learn more about that market and what my team could do to be an effective part of it, I packed my bags and hit the road. By the end of the year, I had visited over 40 prefab factories across the country, from the inland empire of Southern California to the coast of Maine, and many, many spots in between.
Most of the factories I visited were focused on building single-family, wood-frame, low-rise modular homes, but there were a few exceptions. Some were using steel framing, one was all about ADUs and a couple were turning out panelized systems.
Now, I’m not a factory operations expert in the slightest, so I’m not here to dissect that. I work for a company that manufactures rigid polyiso insulation, and my goal is to help modular and other offsite builders make their homes more energy-efficient and weather-resistant. That’s the angle I came in from, and I’ll be sharing my thoughts on how they’re progressing.
But I was also on another mission. As an active member of the Modular Home Builders Association and the Modular Building Institute, I wanted to learn more about where the industry stands as a whole. So, I’ll be sharing some general insights as well.
Hopefully, readers in the modular industry will find my observations useful, and maybe some factory owners and managers will gain a bit of perspective on where they stand in relation to the rest of the field.
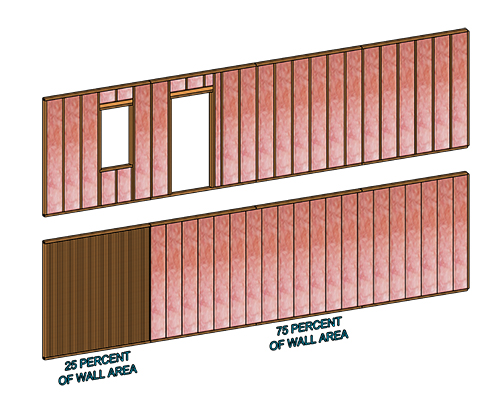
General Impressions
My big-picture impression is that people in this industry are committed to building high-quality homes in the most efficient manner possible. And they’re committed to doing so regardless of the level of technology they’re able to deploy.
There are a ton of factories out there — way more than I initially realized. I counted at least 125 modular operations, many of them small companies that don’t get much press but have been quietly building homes for 20, 30, or even 40 years.
Most of these factories are set up in existing buildings they took over —usually warehouses of one type or another. (One East Coast factory even converted a WWII-era plant that used to make military equipment!) They’ve done a lot of work to make the space functional, like creating new material flow pathways.
There were a few factories that were purpose-built from the ground up, and while they were impressive, they operated at similar levels of efficiency and production as those that had been adapted from existing buildings. This reinforced for me that a well-organized, skilled management team, and a well-trained team on the factory floor, is often more important to a factory’s success than the facility itself.
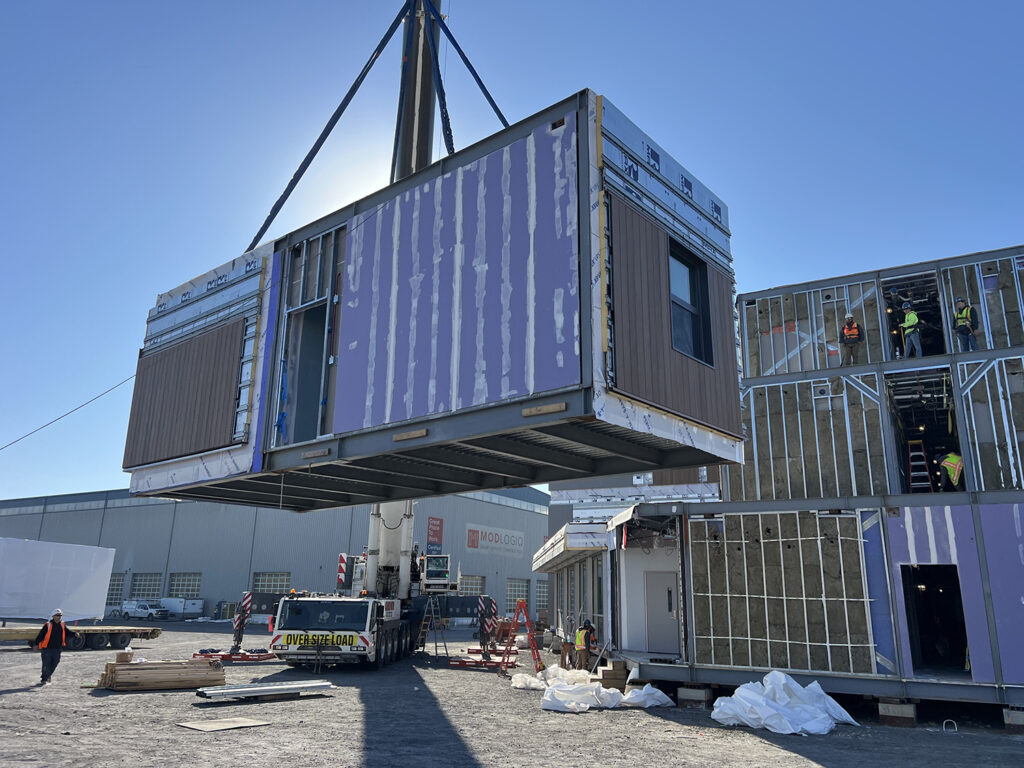
Photo credit: Matthew Zawadski of Construction Ahead
Automation Is Rare
There’s a lot of talk in the industry about automation and robotics. Nampa, Idaho-based Autovol has gotten a lot of press for its use of robots to build their product. Plant Prefab recently opened a fully automated factory in Tejon Ranch, Calif. Semi-custom builder Unity Homes in Keene, N.H. (profiled in this magazine in October 2024) uses a blend of automation and manual labor in its factory.
But those examples are exceptions. Most companies I met with just don’t have the budget for full automation. I did notice several automated saws and can only recall seeing three automated nailers. Instead, nearly everyone I visited was using traditional construction methods, but doing so very systematically, efficiently and with an emphasis on quality.
These manual operations I saw were building in a more advanced manner than any site builder I know of. An uninformed eye might see people putting homes together the old-fashioned way under a roof, but that’s a superficial impression that misses the point.
In every facility I visited, assemblies were precisely measured and laid out. Finished walls were straight and true. Every module moved smoothly from one station to another in a highly organized manner.
In fact, seeing this precision and quality control in person has honestly made me more excited about construction — and my role in it — than I’ve been in years.
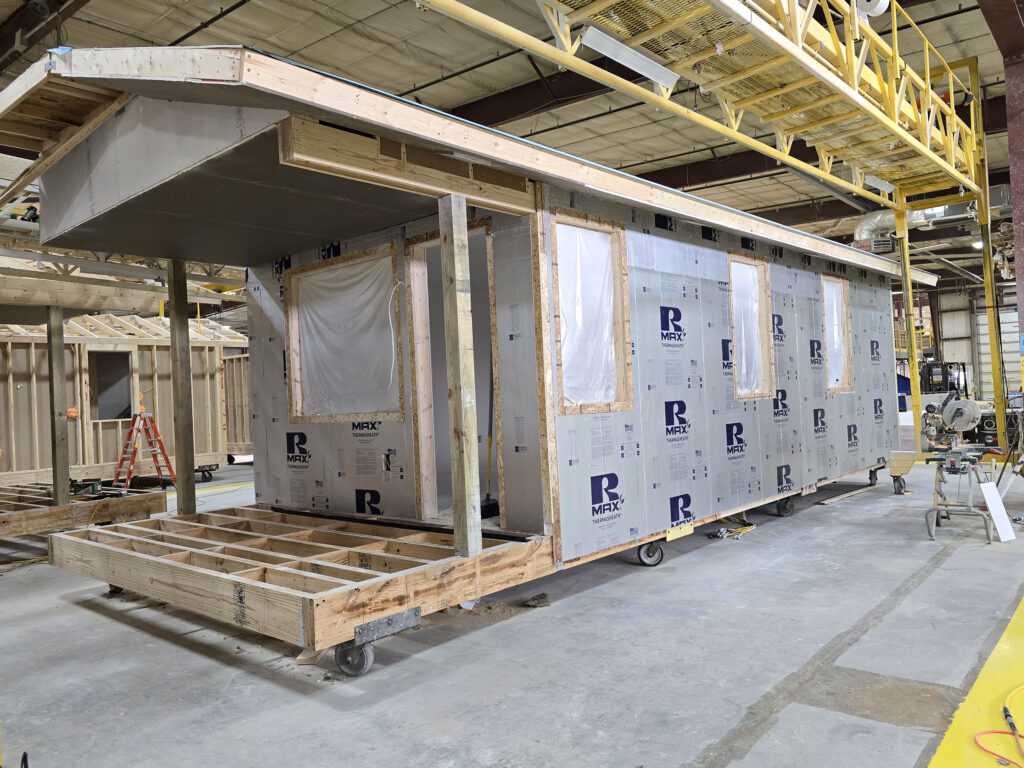
Photo credit: Guy Tuffin at Northstar Systembuilt
Process Improvement Is Big
The companies I enjoyed visiting the most were the ones that embraced process improvement. At least half of the places I visited were open to trying out new ideas and looking for ways to build more efficiently.
Surprisingly, I encountered this willingness more often in the smaller companies, where management understood the value of trying something new, implementing it if it worked, and moving on if it didn’t. These people want to build sustainably and want to meet the new energy codes. The fact that they’re not entrenched in traditional construction seems to make them more open to alternative ways of achieving these goals.
As a general rule, I’ve found the modular manufacturing world to be very thoughtful when considering new processes. This is the case even when their current methods are working well enough, and even when they’ve invested time and money into previous experiments that didn’t pan out.
At the same time, most companies don’t rush into a change, as was the case for an exterior structural insulation product I suggested to one manufacturer. The product would save them three or four trips around the building. It took them a few months to adjust their standard processes and finish the project they were already working on, but once they gave the new product a try, the benefits were immediately clear and it’s now part of their standard specs.
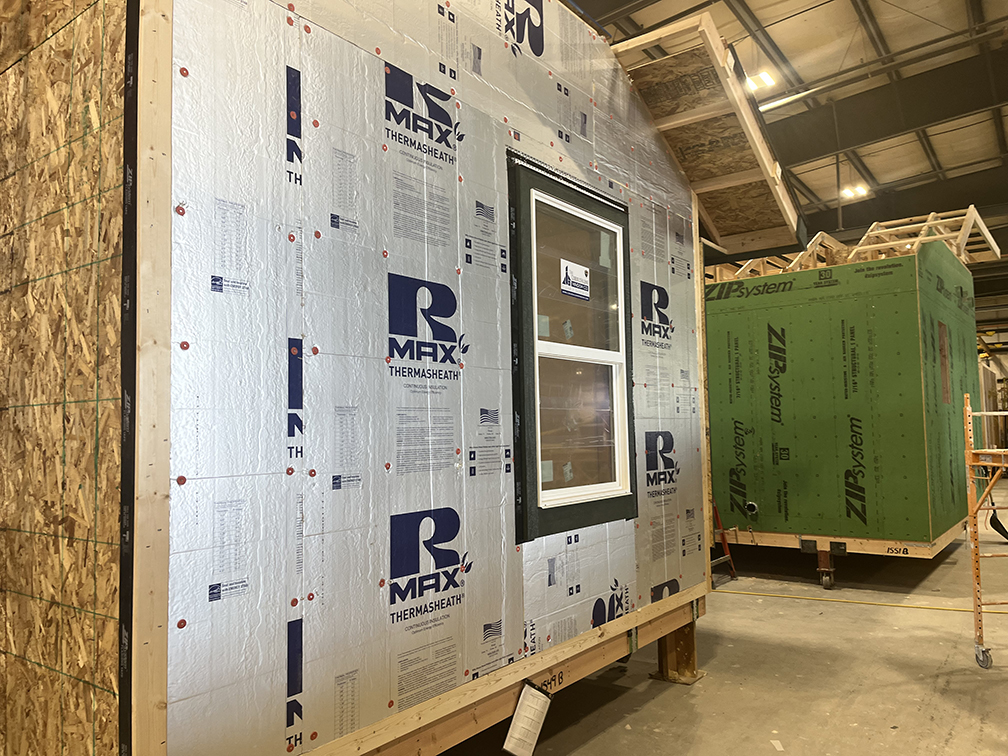
Photo credit: Steve Dubin
Everyone Has Supply Chain Issues
A friend I’ve made in this year is an expert in supply chain optimization. I heard her say at the World of Modular show (held March 2024 in Orlando, Fla.) that “the supply chain struggle is real.” Modular companies need quick, easy and economical access to building materials and products, but satisfying that need can be a challenge.
The truth is that the modular industry doesn’t get the attention it deserves from manufacturers and distributors because it’s still a relatively small slice of the overall market. But on that note, when they are given the attention they’ve been looking for and opportunities for working with material suppliers and producers open up, they need to take advantage of it. I have found that this point is often spoken about, but not as often acted upon.
I’m hopeful this will improve as modular construction continues to grow.
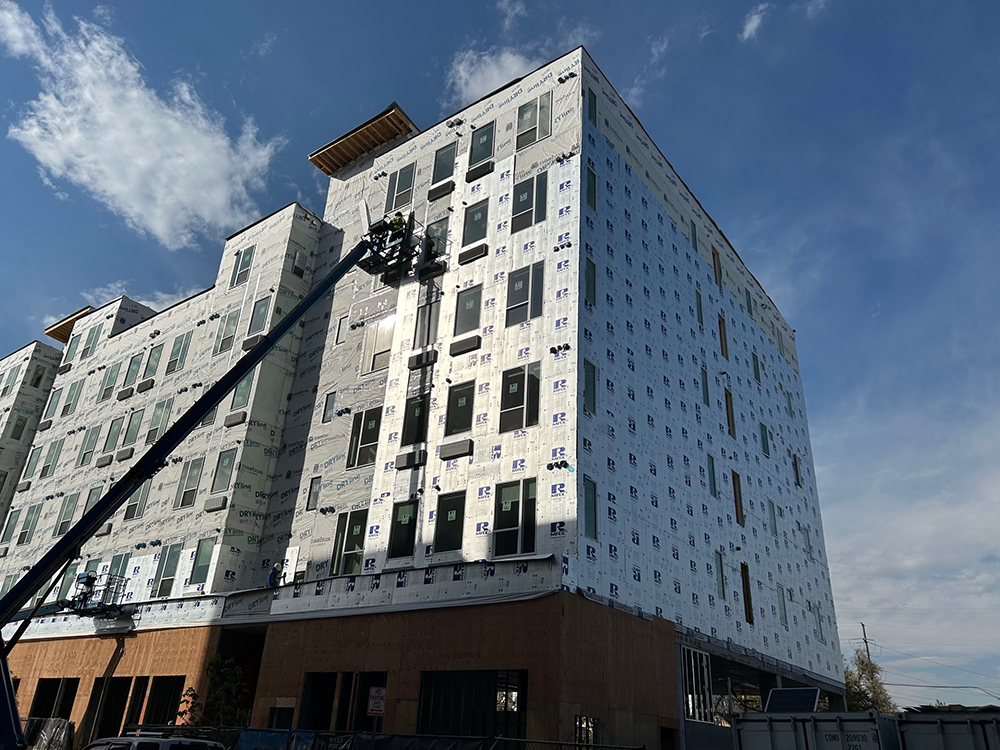
Photo credit: Chelsea Woods from Rmax, a Sika Company
Workforce Issues
Labor shortages are a hot topic these days. The good news is that modular plants can draw from a broader range of workers, and that the controlled environment they offer can be a strong recruiting point.
Most employees I met seemed positive about their work. They liked working in a consistent, comfortable environment — not dealing with extreme heat, cold, or rain like on traditional jobsites. My interaction with these employees made me think that factories’ recruiting efforts might benefit from exposing potential hires to their current workforce.
Interestingly, I found that people with years of site-building experience sometimes struggled to adjust to the more systematic approach of modular factories. For instance, a site electrician might be used to rerouting wires on the fly, but in a factory, everything must be placed precisely, and there’s little room for improvisation.
Some managers I spoke with actually said they preferred hiring green workers for certain roles. You can train someone to follow exact instructions in a few days, and there’s no need to un-teach old habits.
Of course, experienced construction pros do bring a lot to the table. They can be an asset to any plant and shouldn’t be discounted. However, managers should be aware that there will be an adjustment period and that they need to think through how to manage it.
Meeting Energy Codes
As I mentioned, my main focus during these visits was figuring out how factories could build homes with strong thermal performance without driving up costs.
One thing was clear — modular builders understand the importance of high-performance homes. Unlike a lot of traditional builders who just want to meet the bare minimum energy codes, modular companies seem eager to go beyond those requirements. In fact, most seemed to understand that the ability to build a home that exceeds the code’s requirements will be a selling point for them.
That said, energy codes are getting stricter, and have complicated the work. In most parts of the US, residential construction, including modular construction, is subject to the International Energy Conservation Code (IECC). Although some jurisdictions are on the 2015 or 2018 version, most areas around the country are moving to the 2021 IECC. I’ve found that the need to meet these requirements is moving more manufacturers to start using exterior insulation board. In many cases they’re all but impossible to meet without it.
One complication is that exterior insulation increases wall thickness, which forces manufacturers to re-think their wall assemblies. What types of cladding will work with the new insulation? What details will they use to attach it? How will they install windows and doors? How will they detail the deeper window wells?
A bigger issue I never thought of when starting this role is that if the company’s modules are already the maximum size for simple over-the-road transport, adding a couple of inches may result in a module that requires an expensive escort. The factory now must make a choice: eat the added expense or re-design their modules to stay within the maximum width.
Part of my job is helping solve such problems. I was able to work with one factory who initially was going to need to reduce their living space by an inch or so, to avoid additional escort fees. I helped them find a product that met the new code requirement but fell within the tolerances needed to continue shipping their mods as normal, without the need to adjust their design.
Finding Efficiency
Everyone needs more efficient ways to meet the code. This was, and continues to be, the main focus of a lot of my conversations with factory management.
Whether they’re using batt insulation or exterior foam, all the factories I talked to are looking for ways to cut down on trips around the building. Every home needs structural sheathing, thermal insulation, as well as an air and water barrier. The more of those functions you can combine in one product, the more time you will save.
Overall, I am feeling very optimistic about the future of modular construction. Sure, the industry is facing challenges like supply chain issues, labor shortages and the cost of meeting codes. Many are also trying to figure out where and how (and if) to use automation in a cost-effective manner. But the commitment to building high-quality homes is clear, and that makes me excited to see where modular is headed.
I’m looking forward to seeing the next 40 factories and keeping the conversations rolling.
Steve Dubin is a Napa, California-based Business Development Manager for Rmax, a Sika Company, focusing on modular and offsite construction manufacturers. He currently serves on the board of directors for the Modular Home Builders Association. You can reach him on LinkedIn or at [email protected].