This collaboration aims to develop factory-built homes that push the boundaries of energy efficiency at an affordable cost.
- These affordable cottages incorporate technologies like insulated studs, solar shingles and high-performance HVAC systems, all installed at the factory.
- The project is a collaboration between a Virginia developer, a home manufacturer, a university and a government lab. Findings will be made available to the industry as a whole.
- Research goals include gathering insight into how the process of manufacturing factory-built, net zero homes compares to site building.
Together with Accomack County in Virginia, iUnit Communities (iUnit), an Ashburn, Virginia real estate development company, won a half million-dollar grant in September 2024 from Virginia Housing. The grant is being used to manufacture two homes that can perform better than net zero. House designs were finalized in April 2025. Manufacturing, delivery and finishes are scheduled for summer 2025.
We spoke with participants in this project to find out what they’ve learned so far about collaboration and about designing compact, high-performance homes.
Virginia Housing is a not-for-profit organization that aims to help state residents attain quality affordable housing. According to their website, they offer an Innovation Grant designed to “support innovative construction methods that reduce costs and construction time.” Grants can be awarded for a range of efforts, including the development of affordable materials or new techniques that conserve resources while improving quality and efficiency.
iUnit founder Brice Leconte believes that a factor in his winning the grant was his intention to use a product developed by a Virginia-based company. Called Insul-Stud, it consists of a layer of insulation sandwiched between two layers of wood and is meant to replace dimensional studs.
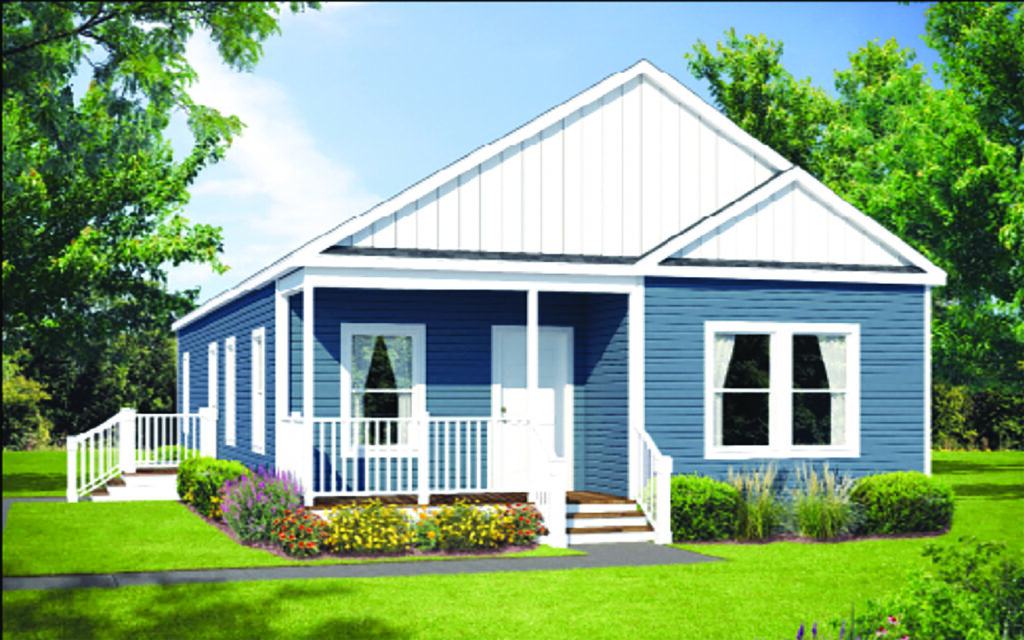
Project Goals
The grant covers the cost of creating two prototype all-electric “Innovation Cottages” — one modular cottage that will exceed residential building codes, and another that’s built to HUD code. There are three main project goals:
- The first goal is to have the cottages as complete as possible when they arrive on-site. Thus, the choice of factory-built homes.
- The second goal is energy efficiency. Leconte’s team has figured out how to build a home in the factory that produces more annual energy than it consumes. “For me, that’s the Holy Grail,” he says.
- The third is affordability. In fact, the cottages are meant as prototypes for affordable housing.
Champion Homes, headquartered in Troy, Michigan, is manufacturing the cottages in their Liverpool and Claysburg, Pennsylvania plants. They’ve done most of iUnit’s manufacturing over the last decade or so. Bryan Phelan is a Director of Business Development at Champion. Phelan says Champion is able to build homes “typically for a little less than stick built.” (That’s in addition to the savings from offsite construction’s shorter timeline.)
He adds that it’s hard for busy companies like his to innovate, however. “We’re focused on the day-to-day business of building houses. This grant has given us time to focus on zero-energy innovation.” He goes on to note that the ability to build low-energy homes is needed to help them grow their market share. “One of our major competitors, Clayton Homes, is well into the zero-energy market, and Champion needs to be too.”
The project’s research partners are Virginia Tech (VT) and the National Renewable Energy Laboratory (NREL).
Philip Agee, Assistant Professor in the Department of Building Construction at VT, and Associate Director of the Virginia Center for Housing Research, notes that grants like this reduce some of the risk of innovation. Crucially, Virginia Housing wants the lessons learned to be shared with the broader industry. “So, everyone can benefit from their investment,” Agee says.
Sharing information will be one of NREL’s roles. According to NREL Building Science Research Engineer Nick Cindrich, one of his lab’s roles will be to “help propagate the results through widely used sources like the Building America Solution Center.”
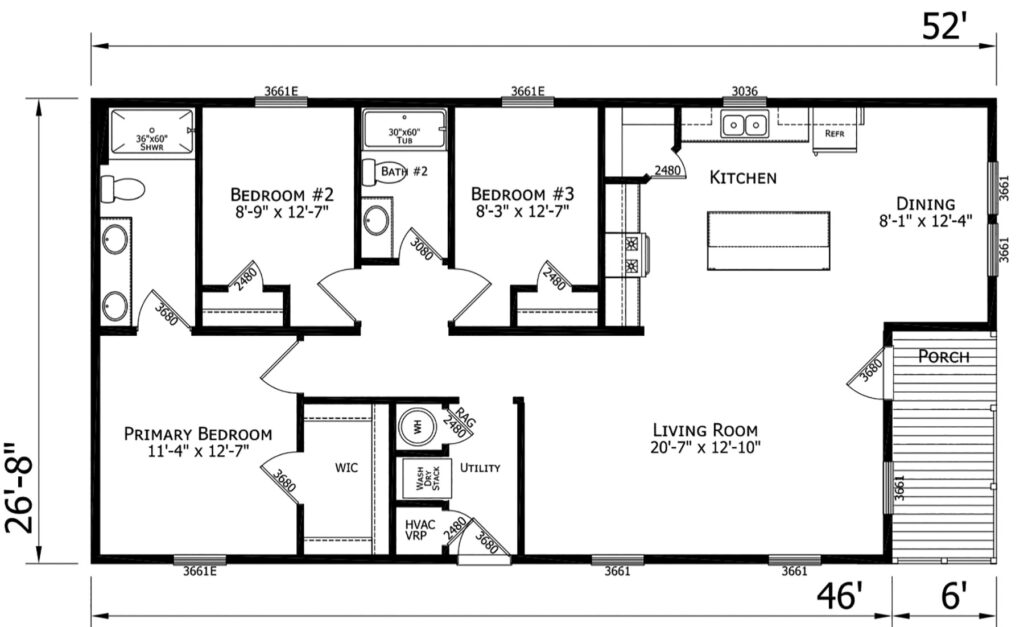
Cottage Design
The innovative products used in each home include the Insul-Studs, as well as solar shingles, a packaged HVAC system and a smart electrical panel.
Leconte explains that Champion wasn’t able to install traditional rooftop solar panels in the factory. They wanted ceilings at least nine feet high, and the overall height of the units is determined by limits on transportation. There simply wasn’t enough height leeway for solar panels, so, instead, the Champion factories installed solar roof shingles on both homes.
The shingles are made by GAF Energy, which describes them as the “world’s first nailable solar shingles.” Leconte explains that the solar material is incorporated into the roof shingle itself. “About 40% of the roof will have solar shingles and the rest will be regular shingles,” he says.
NREL was tasked with “identifying a packaged [high-performance] HVAC system,” Cindrich says. “We’ve analyzed the airflow and performance of the [HVAC] system to confirm it will meet comfort standards,” he adds.
Although both homes will be Energy Star certified, Cindrich says that the HUD-code home won’t offer the same thermal performance as the above-code modular unit. “So, to meet net zero, the HUD home will have to produce more energy with solar shingles.”
Both homes will also have a Leviton smart electrical panel installed, which will allow the team to remotely monitor whole-house energy consumption and production, according to Leconte. The device provides fine-grained data that includes the energy used by specific appliances.
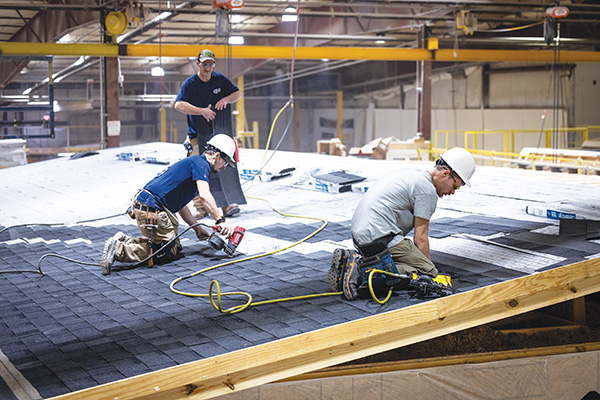
Collaborating Successfully
VT’s Agee says that although working with researchers at another institution can sometimes include a bit of a turf war, “this project has been very collaborative.” He says the main reason is that “everybody’s in it for the right reasons. Everybody wants a good [outcome].”
Participants in any project come to the table with different skills and different areas of expertise. The challenge is how to get them working harmoniously as a team. “A lot of it comes down to building trust,” says Agee. That can be a challenge when team members are interacting virtually rather than face-to-face. To overcome this, he recommends that everyone specifically agree not to take it personally when someone disagrees with them. “Be flexible and adaptable,” he advises. “Check your ego and be willing to learn. Have a positive attitude.”
Champion’s Phelan says that working on this project hasn’t been unusual for his company. “We’re all trying to achieve the same goal, which is designing, building, installing the house — it’s not very different than what we do normally.”
The only significant difference is the inclusion of a few new products. That’s because Champion had to take the time to understand each product, and then had to determine if it could work in their builds. “For instance, we had to find out whether it was feasible to install the solar shingles in our plant,” says Phelan.
Patience has also been a necessity on this project. Leconte says that “getting all the equipment and product manufacturers to give us the specs and the drawings took lots of time.”
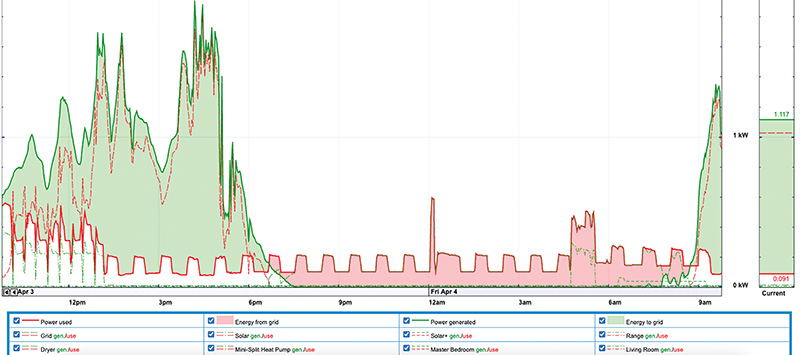
Credit: Philip Agee
Design Lessons
One important difference with the cottages when compared to average homes, was the location of the ductwork. Phelan says that ordinarily, “duct work goes up in the attic, or [in a basement or crawlspace].” But he’s learned that, for a zero-energy project, “the HVAC all has to be inside in a controlled airspace.”
Agee says that although none of the materials or systems being used are “exotic,” integrating them into the homes requires a lot of attention to detail. For example, he mentions that “when you build more airtight buildings there’s a risk of higher indoor humidity.” A decade ago, a typical heat pump would’ve dealt with moisture removal, but they have since become more efficient and run for shorter periods. That efficiency is good, but the problem now is that they don’t run long enough to remove the moisture from internal sources (like people and hot showers) and moisture that comes inside through opening windows and doors.
To address the humidity issue, Cindrich turned to research that NREL has been doing with iUnit on a modular apartment (see “NREL Tests a Modular Apartment” in the September 2024 issue). The lessons learned about modular thermal performance and air infiltration are proving useful for the single-family Innovation Cottages and helped the team choose an appropriate HVAC unit.
“The unit we selected has a reheat coil inside that increases the system’s ability to dehumidify when the cooling load is low in a small, air-tight structure,” says Cindrich. “The effect is that the system can dehumidify for longer without overcooling the space.” He explains that, with a reheat coil, “left over energy from the refrigeration cycle — not a separate energy source — warms the outgoing air and slows down room cooling until a humidity target is met.”
The HVAC system also conforms to another project goal: “To be completely installed and commissioned in the factory, eliminating the need to install an outdoor condenser when the unit is placed on-site,” Cindrich adds.
Another conclusion the team reached during design was to rule out continuous exterior installation. “Exterior insulation is high performing and robust, but it’s difficult and time consuming to stitch together,” Cindrich says. The Insul-Stud product “provides the same thermal performance as continuous insulation” but is easy to build with in the factory. This product also reduces insulation material used by 40%.
Lessons for a Future Project
Once the homes have been occupied, Cindrich says that the researchers will “be collecting data about interior temperature and humidity levels, moisture in the crawlspace, and energy consumption.” In addition, they will be surveying residents to gather qualitative data to supplement the quantitative findings, and to understand people’s acceptance and use of this type of housing.
They are also analyzing the construction process, from design and permitting, all the way through to occupancy. This will include:
- Comparing the process of producing net-zero housing in a factory to that of site building.
- Comparing the cost, schedule and quality of offsite and on-site production for this type of housing.
- Documenting the challenges and opportunities for producing this type of housing, including regulatory and policy issues.
The information the researchers gather from the Innovation Cottages will also be fed to computer models that estimate the performance of a future iUnit development on a 65-acre site in Strasburg, Va. “We’re planning to place 212 of these cottages there, plus a 7-acre community solar farm to produce energy for the homes,” Leconte says.
He says that the Strasburg site has probably another year or year-and-half of entitlements. The Innovation Cottages will have been occupied for a while by then, so there will be plenty of data and resident feedback to use when tweaking designs.
Leconte’s personal goal is to continue improving the energy-efficiency of factory-built homes. In fact, he describes that as his life’s work. “I’ve spent countless hours, sometimes waking up at three in the morning to get things done. And you spend a lot of time working on things that, in the short term, don’t make financial sense. But if you’re committed for the long term, then it’s worth the investment.”
Zena Ryder writes about construction and robotics for businesses, magazines, and websites. Find her at zenafreelancewriter.com.
Photos courtesy Champion Homes, except where noted.