The missing link is the ability to get factory and field on the same schedule.
- Lean isn’t just about the factory or the field — it’s about what happens between them. A disconnect can create chaos.
- Foundations for synchronization include Takt planning and DFA (Design for Assembly). Useful tools range from BIM to cloud-based tracking, to digital Gantt charts and punch lists, to in-person meetings.
- One builder used this system to increase crane time efficiency to more than 90 percent. This eliminated rework and got the job done ahead of schedule with the lowest punch rate the builder had ever seen.
In our first two articles, we tackled a common problem in offsite construction: the disconnect between factory precision and field execution. We looked at how Lean thinking helps reduce waste and create flow on the jobsite through tools like 5S and visual management. But what happens when the jobsite is dialed in and things still go wrong?
It usually comes down to timing.
Even with the best field processes, crews can’t be efficient if the factory and the field are marching to different rhythms. Modules arrive too early and get in the way, or too late and leave the crane sitting idle. Sequencing gets jumbled. Information breaks down. The result? Delays, rework and missed opportunities.
The third piece of the Lean field equation is synchronization: aligning offsite production with on-site execution so the right work happens in the right place, at the right time. In this article, we’ll explore how to bridge that gap using simple principles, better communication and tools that keep the whole team moving as one.
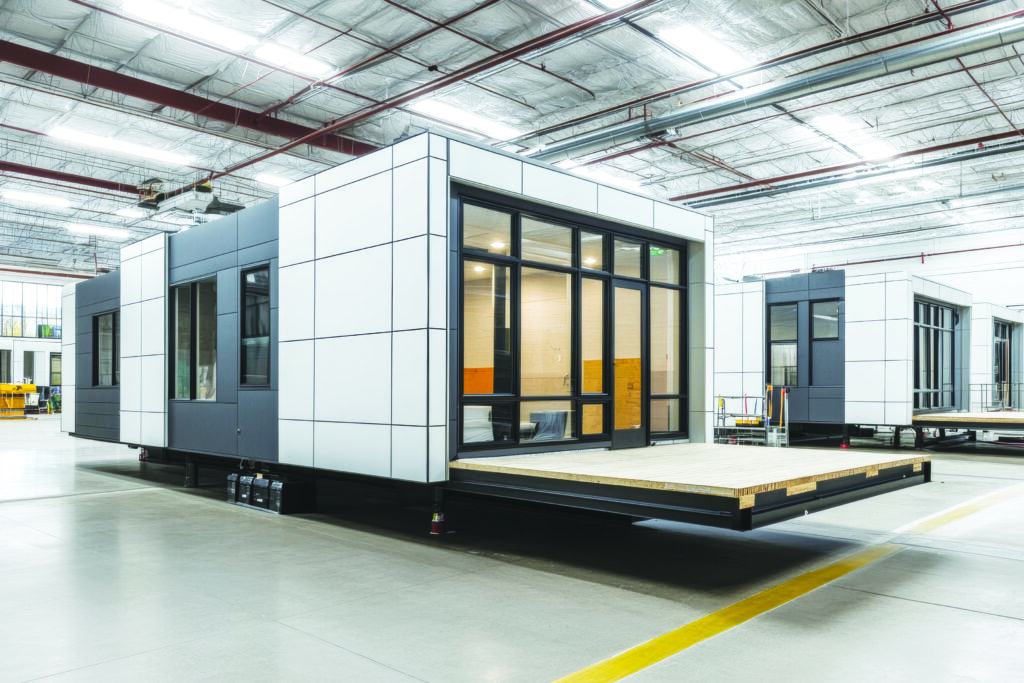
When Factory and Field Don’t Sync
Even when both teams are doing their jobs well, the disconnect between offsite and on-site operations can create chaos. One of the most visible breakdowns is crane inefficiency: a crew stands by waiting for modules that haven’t arrived, or worse, a module that’s delivered early ends up sitting on-site while crews catch up — wasting both crane time and storage space.
Mismatched sequencing is another common issue. If factory production doesn’t match the field installation plan, modules or panels can arrive in the wrong order, disrupting workflow and forcing out-of-sequence work. This often results in temporary fixes, redundant handling and rework.
Communication breakdowns also show up in subtle, but costly, ways. The field crew might not know where the next delivery is staged, or they might discover at the last minute that a critical element is missing or incomplete. Meanwhile, the factory may be operating under outdated site conditions or a misunderstood installation schedule.
These problems aren’t caused by laziness or incompetence, they’re caused by misalignment. Without shared systems, routines and feedback loops, even highly capable teams can find themselves out of sync. And when that happens, everyone pays the price in delays, frustration and lost profit.
Fortunately, Lean principles can help eliminate these disconnects and promote true synchronization.
Laying the Lean Foundations
At the heart of Lean is the concept of flow — the uninterrupted movement of value from one process to the next. In modular construction, that flow needs to extend from the first cut in the factory to the final screw turned on-site. Synchronization is what enables that continuity.
One of the most powerful tools for achieving it is Takt planning. Takt planning is a scheduling method that sets a steady, repeatable pace for production and installation. It defines the interval — or “Takt time” — at which each unit or batch should move through the process. By aligning factory output and field capacity to that pace, Takt planning reduces overproduction, bottlenecks and idle time. Instead of pushing product forward as fast as possible, work flows at a consistent, reliable tempo that both teams can plan around.
Equally important is Design for Assembly (DFA). DFA is the practice of designing modules and components with the installation process in mind. That means simplifying interconnections, using standardized fastening methods, minimizing field-applied finishes and reducing the number of ship-loose parts. The goal is to make modules easier and faster to assemble on-site, with fewer surprises and fewer tools. Good DFA doesn’t just reduce installation time — it lowers the risk of damage, error and rework. For example, electrical connections may be designed with plug-and-play harnesses that snap together on-site, eliminating the need for field wiring.
But synchronization isn’t just about technical processes — it also requires human ones.Pre-installation coordination sessions, held between factory planners and field supervisors, are critical. These meetings align sequencing, identify red flags and help both sides understand the real-world constraints the other is dealing with.
Together, these practices form the backbone of synchronization. They turn disconnected operations into a unified value stream and set the stage for using digital tools to make that alignment even stronger.
Tools to Make This Possible
While Lean principles establish the framework for synchronization, digital tools and communication routines are what make it practical — and scalable. Modern technology can eliminate many of the traditional friction points between offsite and on-site teams by providing shared access to the same information, in real time.
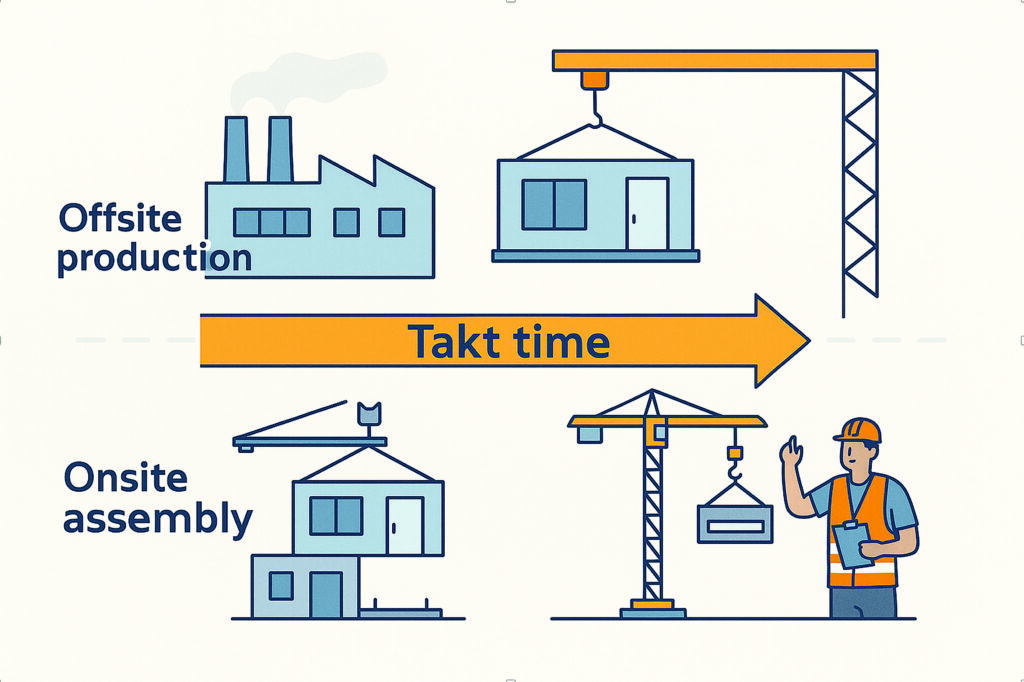
At the center of this toolkit is Building Information Modeling (BIM). When properly implemented, BIM serves as a single source of truth that integrates manufacturing data, sequencing logic and installation requirements. Crews in the field and engineers in the factory work from the same model, reducing guesswork and miscommunication.
Supplementing BIM are cloud-based trackingtoolsthat monitor production status, delivery logistics and site readiness. These systems allow both teams to see when a unit was completed, when it shipped and what dependencies need to be met before installation. Some firms even integrate GPS-based delivery tracking and photo documentation so everyone — from project manager to forklift operator — knows what’s coming next.
Equally important are the routines that keep people in sync. Weekly coordination calls, shared digital Gantt charts and mobile-accessible punch lists all support alignment. Standardized delivery labels and QR-coded shipping manifests help ensure that components are matched with the right locations and crews.
One builder implemented a simple, but effective, system: every module has a laminated install sheet attached, complete with crew notes, staging instructions and a QR code that links to the real-time project board. The result? Fewer phone calls, faster decisions and tighter installs.
The goal isn’t high-tech for its own sake — it’s clarity, consistency and connection. The right tools make it easier to do the right thing, every time, across the whole delivery chain.
This Builder Got It Right
On a recent multifamily modular project, the builder was determined to close the gap between factory and field. They implemented a Takt plan that defined module delivery and crane scheduling with near clockwork precision. Every module was labeled with install order, drop location and staging instructions.
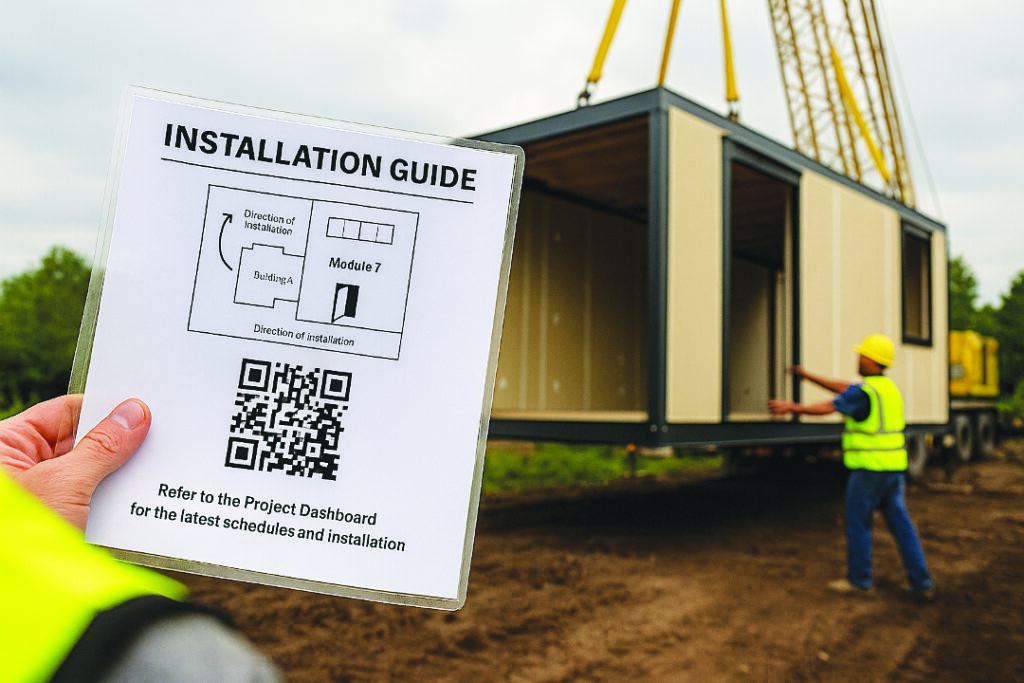
Before the first delivery, the site superintendent and factory team held a joint walkthrough using a shared BIM model to review sequencing. Field crews used mobile tablets to track module status and readiness, with live updates pushed from the factory floor. Deliveries arrived just in time — neither early nor late.
The result? Crane utilization exceeded 90 percent efficiency, with minimal idle time. The field team was able to complete stitching, MEP tie-ins and finish work without rework or disruption. The project finished ahead of schedule, with the lowest punch rate the GC had seen on a modular build.
Synchronization didn’t require massive investment — it just took deliberate planning, strong communication and the discipline to follow the plan.
Takeaways and What’s Next
Synchronization isn’t a one-time coordination meeting — it’s a system. A system built on shared expectations, clear information, reliable routines and mutual trust between the factory and the field. It’s not about speed alone — it’s about timing, sequence and rhythm.
When modular manufacturers and field teams truly sync up, the whole operation flows more smoothly. Crane time is maximized. Crews are ready. Deliveries land where and when they should. Waste drops. Quality rises.
In the next article, we’ll take the next step: how to keep that rhythm going through Lean scheduling methods like Takt time, crew balancing and continuous improvement cycles that keep offsite and on-site in lockstep, day after day.
Because the job doesn’t end when things are “on time” — it ends when everything is in flow, and Lean makes that possible.
Daniel Small helps offsite manufacturers increase factory throughput and eliminate waste using Lean strategies. As a specialist in Lean for offsite construction, he optimizes offsite production for scalability and efficiency. Contact him at 719-321-1953 or [email protected], or visit www.DaVinciConsulting.co.