Colleges need more housing units, and modular is proving itself to be a viable solution.
- Modular construction is a timely solution to the student-housing shortage faced by colleges and universities, as it can be completed in time for the opening of the school year.
- Modular construction can deliver buildings 60% faster than conventional construction.
- Student housing lends itself well to modular construction because of standardized features such as unit sizes, room sizes and number of sinks per unit.

Photo credit: Signature Building Systems
Student housing is in short supply. Enrollment in colleges and universities far exceeds available housing, and the obstacles to building new include tight financing, budget constraints and rising construction and land costs. Schools are finding that modular multifamily buildings can be a quick, high-quality, efficient solution.
“Universities now are much more attuned to higher efficiency construction,” notes Tom O’Hara, Manager for Major Projects at Signature Building Systems in Moosic, Pa. Over the past five years, O’Hara estimates that 20 to 25% of Signature’s output has been student housing.
With student housing, there is always a deadline that corresponds to the beginning of the school year. “Campuses guarantee housing to students via their contracts of admission, and if the housing isn’t ready the schools are on the hook to find hotel rooms for those kids,” O’Hara explains.
Kari Shotwell, Business Development Manager for CRATE Modular (CRATE) in Carson, Calif., points out that modular construction can deliver buildings 60% faster than conventional construction. It also causes minimal disruption to schools and communities because there is less traffic and noise compared to a traditional jobsite. “Factory-built construction is more controllable, with precise inventory management and less material waste,” Shotwell says.
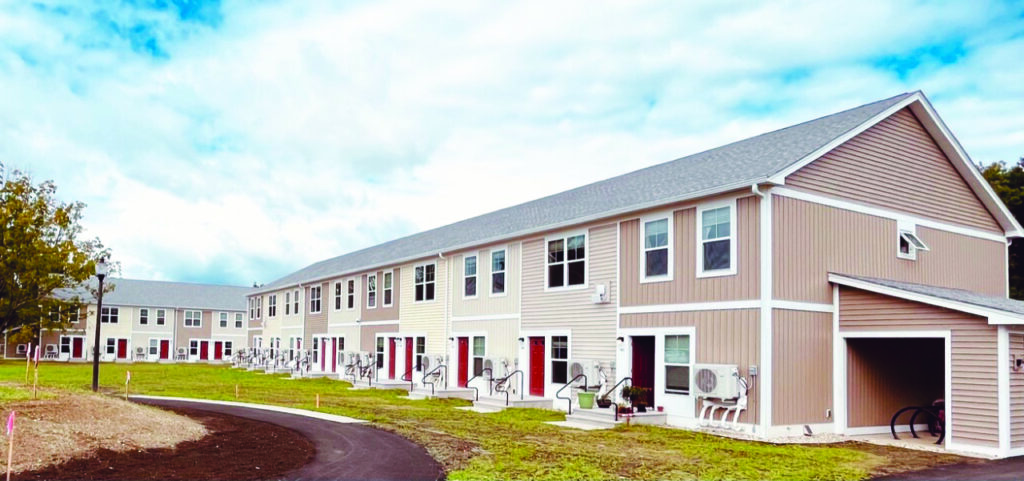
Photo credit: Signature Building Systems
CRATE is collaborating with architects and developers on designs for the workforce and homeless populations that will also serve the student housing market. Examples include El Cerrito Affordable & Supportive Housing, a project that repurposes shipping containers as housing units. LPA Design Studios (LPA) in Irvine, Calif., is the architect on that project.
A recent bond proposal by California Gov. Gavin Newsom, which includes funding for community colleges, has spurred a flurry of design and development activity in the state, says Shotwell. LPA and CRATE are presently designing student housing for a community college. “The [college we] will be working on is one of the very first community colleges to move forward under this new bond,” she says. “It will be built on land donated to the school.”
CRATE and LPA are armed with information from several community colleges that were surveyed about their needs and wants for student housing. All agreed on studio and one- to three-bedroom units (with the possibility of four), and bathrooms and kitchens inside each unit. Some colleges wanted a community kitchen area on the main floor as well. Bike rooms, community spaces for socializing and offices in the building for school counselors were also desirable.
Several schools wanted three- to four-bedroom units for students who have families. “There is also chatter about students who need to take care of their parents, who are ill,” Shotwell says. “They might be eligible to move into one [of the larger] units.” The colleges, she adds, “are looking at every possible situation for students who want to attend college but may have some challenges holding them back.”

Photo credit: Signature Building Systems
Product Consistency
Student housing lends itself well to modular because unit and room sizes are consistent, says Marissa Kasdan, Assoc. AIA and Director of KTGY’s Research and Development Studio in Washington, D.C. (KTGY is a national architecture, branding, interiors and planning firm). “Typically, our developer clients are looking for everything to be [the same], from the length of the bar in the closet to the number of sinks in the unit,” Kasdan says. “They want to be able to rent a similar space to each student, making it an easy leasing process. By modularizing the units, we can build all [their specifications] into the design.”
Signature provided modules for the recently completed University of Massachusetts Amherst Family Housing project, which comprises 150 two-bedroom, one-bathroom apartments. The project replaces an old apartment complex that housed married faculty members, says O’Hara.
“The nature of the undergraduate and post-graduate population has changed so much that there are a lot of folks with kids that need housing,” he says. “Amherst is a very expensive town and there just isn’t any housing you can afford if you need multiple bedrooms.”
UMass Amherst Family Housing was planned as a low-density neighborhood rather than a traditional, monolithic dormitory building. There is green space for children to play and parking close to the units. The diverse renter profile includes undergraduate students, graduate students, teaching assistants, single parents with one child and married couples with one or two children.
Signature produced 315 modules, plus 15 panelized storage areas, in the Moosic, Pa. plant, and provided transportation and erection. Site work, foundations and on-site finishes were done by Suffolk Construction, Boston.
The project is rated LEED Silver and complies with the Massachusetts Energy Stretch Code, which requires individual blower-door testing as well as high-efficiency MEP performance. O’Hara says the construction process utilized 67% less energy than traditional construction and reduced landfill waste.
“We achieved full project certificate of occupancy 14 months after the first module went into production,” he says. “You can’t do that with site construction.”
For developers who thoroughly understand the local market, modular and student housing are an unbeatable combination. “It’s the perfect way to bring product to the job,” O’Hara says.
Susan Bady is a freelance writer based in Chicago, Ill., who focuses on residential and commercial design and construction topics including sustainability and building technology.
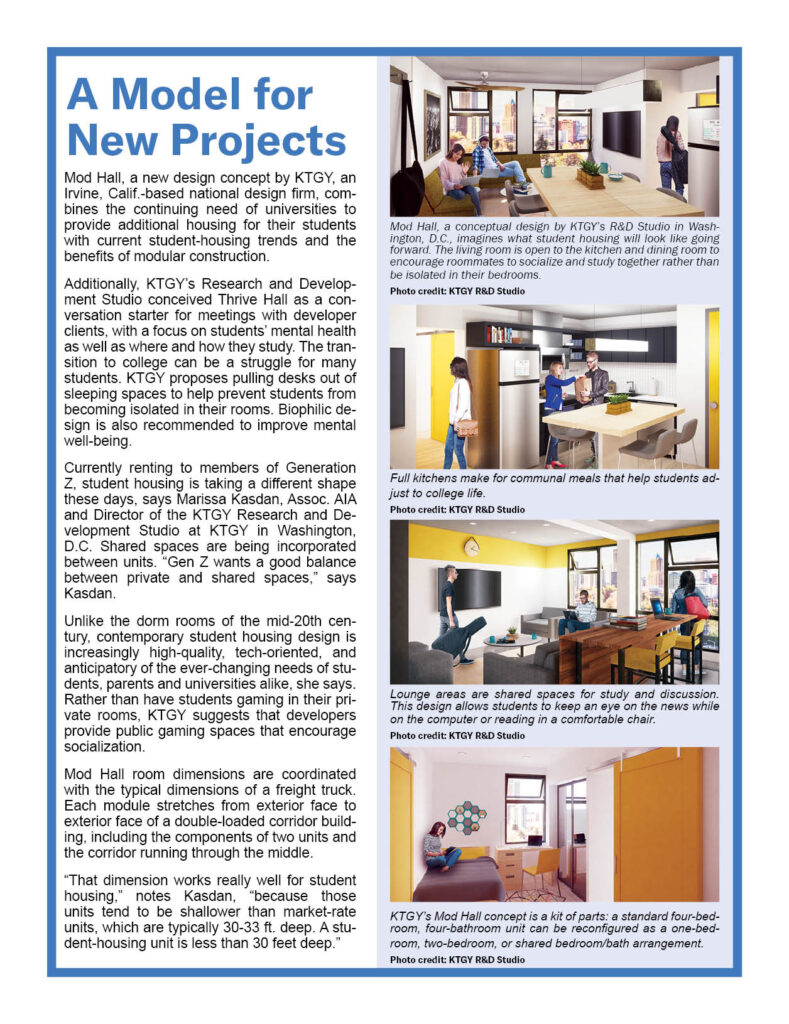