IBS show home aims to open conversations with builders and developers on how modular construction can help them.
- Most would assume that this home was custom built on-site; a fact the manufacturer hopes will open doors with builders and developers.
- It was adapted from an architect’s plans. The tweaks needed to make it modular did not change the original design.
- A home like this can be built to meet any set of code requirements.
- Modular efficiencies can help builders and developers offer small, high-quality homes to people with limited budgets while still making a profit.
It’s not uncommon for professionals and homeowners alike to have preconceptions about modular construction. Most of these are inaccurate — they’re based on a misunderstanding of the value and quality today’s modular factories can deliver.
Greenwood, S.C. Impresa Building Systems wants to challenge those preconceptions with its new Carolina Cottage. This compact modular home will be open for tours at Pro Builder Show Village during the 2023 International Builders Show (IBS) in Las Vegas, Nevada.
Their goal with this home is to demonstrate modular’s design, construction and quality possibilities, while also showing the business advantages it offers to the builder and developer. Some of these advantages may surprise you.
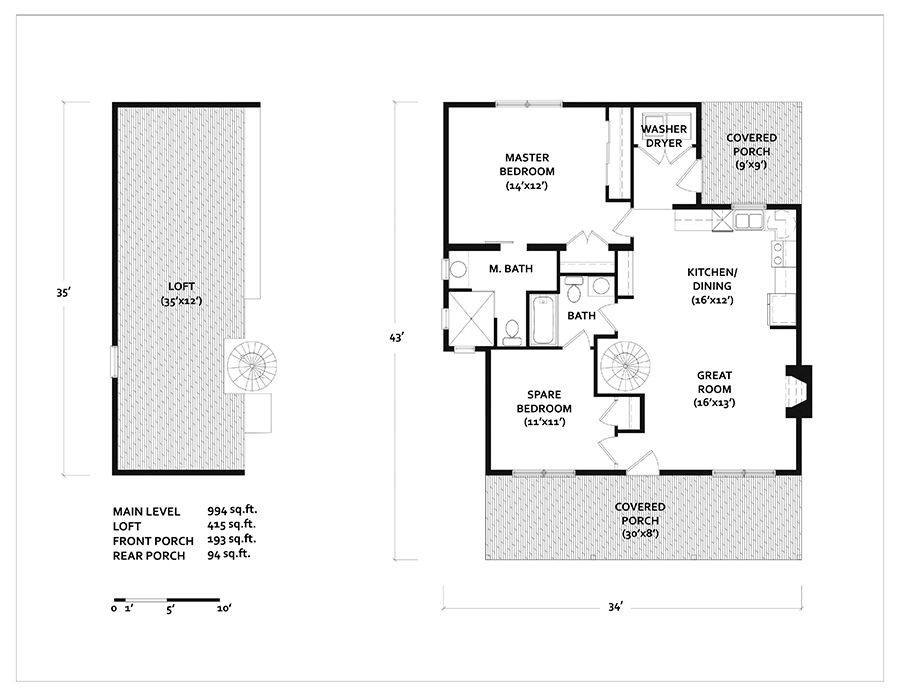
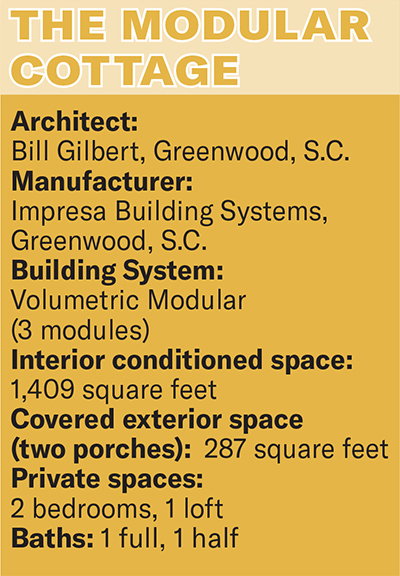
Good Design
The Cottage is a 1,400-square-foot, two-bedroom home aimed at second-home buyers, retirees and young couples. Impresa has already placed several of them on lakefront properties in the Carolinas, but they believe there’s a much wider geographical market for a home of this type. It would be at home in a variety of settings, from a lakeside or mountain property to a small infill lot.
It’s a real gem: a simple, beautiful floor plan that includes a great room with a full kitchen and living/dining area, as well as two bedrooms and 1.5 baths. Thanks to the steep-pitched roof, there’s a cathedral ceiling spanning the common areas and a loft over the bedrooms. There are also covered front and back porches, both built in the factory and integrated into the modules.
A lot of people, when they see a small home with a steep roof and covered porches, automatically assume it’s site built. That’s the point. The fact that it’s modular opens conversations with builders and developers.
In fact, Impresa hopes that its presence at IBS will do more than bring in sales of this particular model (though they would obviously like that). A bigger point they want to make is that there’s a growing market for small, thoughtfully-designed homes and that modular is a great option. “The Cottage fits nicely into the upper-end square footage of small home design,” says Darin Zaruba, Impresa’s Head of Capital & Investor Relations. “It’s right-sized for many of today’s buyers.”
Another point is about the design process. That process will always be smoother if the architect, from the beginning, knows that the home will be modular because the home can be designed from scratch to be built in the factory’s line. However, that’s not always necessary.
A good factory will be able to work with just about any design — a fact that many people still don’t know about modular. The Cottage is being offered as a production home, but it’s based on a home designed by South Carolina architect Bill Gilbert for a lakeside community. “When we opened our factory in Greenwood, a developer brought this plan to us and said ‘I would like something like this built as a modular’,” says Zaruba.

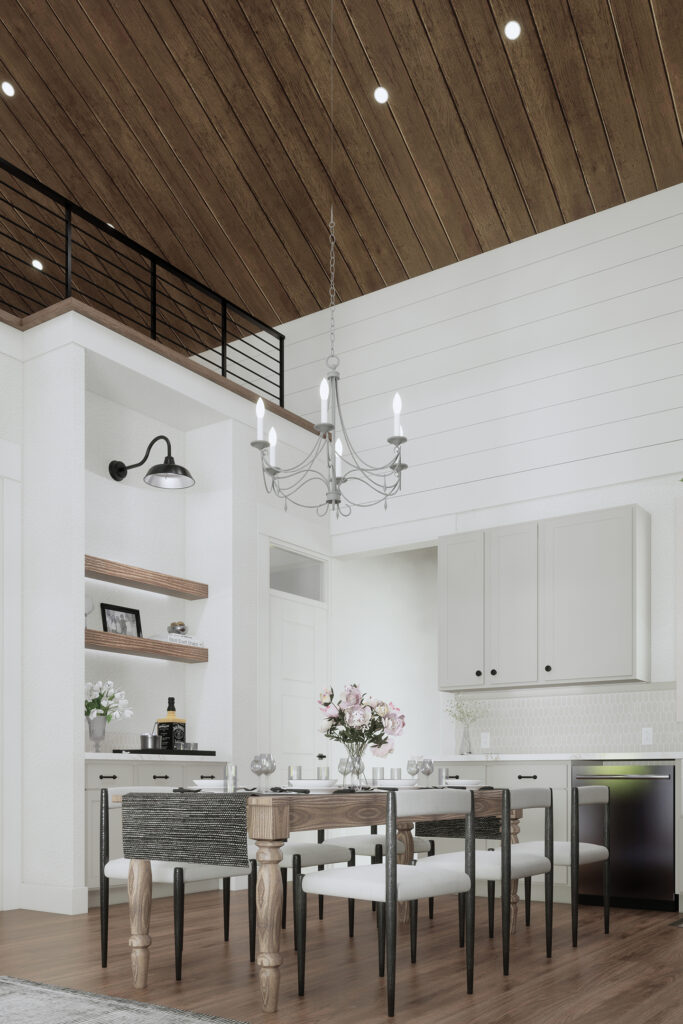
Going Modular
The “modularizing” of a pre-existing design can require some tweaks because factories must think of homes in terms of modules, or boxes. How many modules will be needed to build it? How can the modules be configured to minimize the amount of work that will need to be done on-site? Modularizing can include things like changing some dimensions, moving some walls, or even flipping a bathroom. And it all must be done with as little impact as possible on the home’s look and feel.
This work obviously wouldn’t be cost-effective to do on every individual house. If you’re a builder or developer, the goal should be to settle on a final modularized plan (and perhaps a few variations), then make it part of your standard portfolio. “You’re going to want the factory to build it over and over,” says Zaruba.
Financial Benefits
While a modular factory can offer the same look as a custom home, the numbers can be a lot more attractive. Materials will probably cost the same, but you will need less labor. And because the efficiency of the factory ensures that homes get finished more quickly, carrying costs are lower.
“With modular, you push much of the building overhead to a factory,” says Impresa President Ken Semler. “The factory becomes your biggest supplier. They take over procurement and purchasing and do much of estimating. This eliminates a lot of personnel headaches.”
Those cost savings mean that the builder or developer can make a profit while also offering a lower purchase price to the homebuyer, which will qualify more people for a mortgage. “With the economic downturn, a lot of people can’t be spending $1 million or even $1/2 million on a house anymore,” says Zaruba. “But they still want high-end amenities and a unique look.”
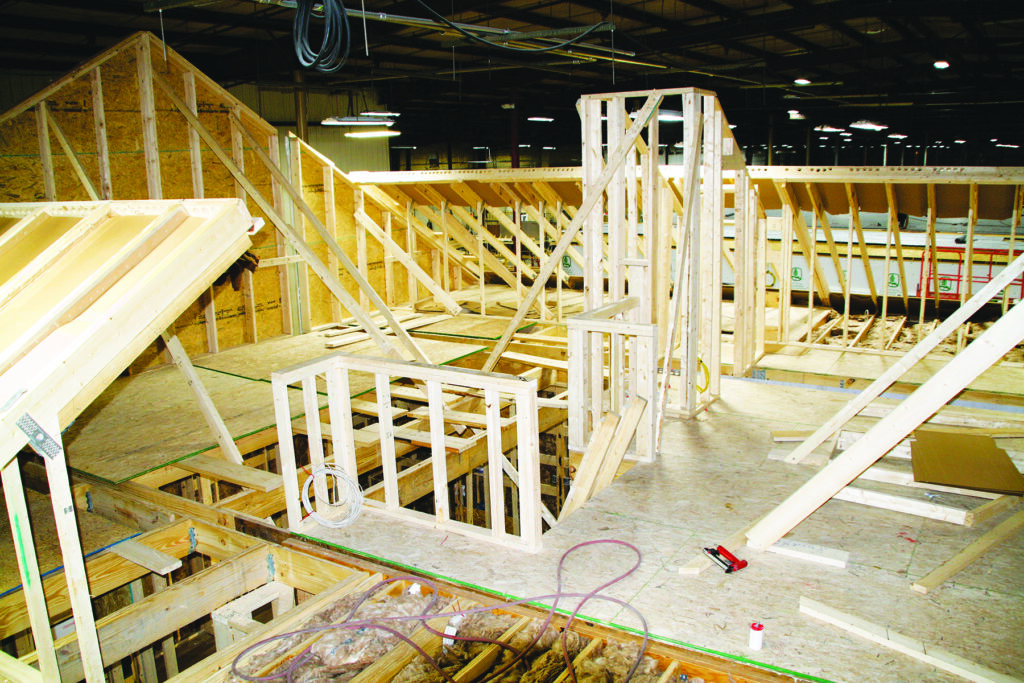
Quality Specs
The quality available from a good manufacturer may come as a surprise to some. For instance, products in the Carolina Cottage include Shaker-style solid wood cabinets, luxury vinyl flooring and cellular PVC exterior decking. Exterior walls are framed with 2x6s placed 16 in. OC.
Homes are built out of the weather. “Compared to site building, floors never get rained on. That means fewer mold and mildew issues,” says Semler.
Modules are built in assembly-line fashion, moving through the factory and stopping at several stations. Workers at each station do a specific set of tasks.
Each station has a protocol for how the work needs to be done and each station includes a quality inspection. In addition, the plant is overseen by an in-house QC manager, as well as a third-party inspector, the latter of whom certifies homes much the same way the FDA certifies meat. (Several third-party inspection companies in the US offer this service. Impresa uses one called NTA.)

Workers can frame and detail the home to meet any type of code, whether it’s a cold northern climate that requires a low HERS rating, or South Florida, where extra structural reinforcement is needed.
Despite all these advantages, developers who haven’t used modular in the past may still be apprehensive. Zaruba says that’s the biggest reason Impresa has chosen to show this particular home — he believes that a small, high-quality home like the Carolina Cottage is a good way to test the waters. “If you’re a builder/developer, it’s a low-risk opportunity to dip your toe into modular.”

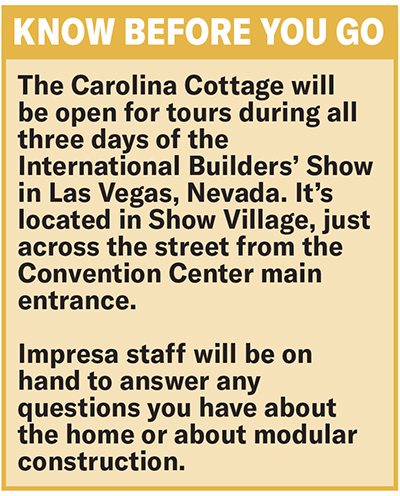