This fully finished modular home was printed indoors then delivered to the jobsite.
- A University of Maine research team has developed a wood-fiber composite material that is completely bio-based and plastic-free.
- They used the composite to print a small house comprised of four modules, which were delivered to the site and then bolted together. Everything was printed, including the roof.
- The team is planning a second home, incorporating improvements based on the data collected during the year the home has been in place.
Dr. Habib Dagher is the Principal Investigator on the BioHome project, which has produced a new type of 3D-printed, single-family modular home. Readers of this magazine are likely familiar with the typical printing of 3D houses, which happens on the jobsite and uses concrete. By contrast, the BioHome was printed offsite in an indoor facility, using a combination of wood fibers and a bio-based resin.
Dagher is the Director of the University of Maine’s Advanced Structures & Composites Center, a National Science Foundation funded research center housed in a 100,000 sq. ft. laboratory. More than 400 people from 35 different disciplines work in the lab, and it was this multi-disciplinary team that developed, designed and printed the BioHome.
We asked Dr. Dagher about the material the team used, the printing process, and what they have learned about the home’s performance during the year since it was built.
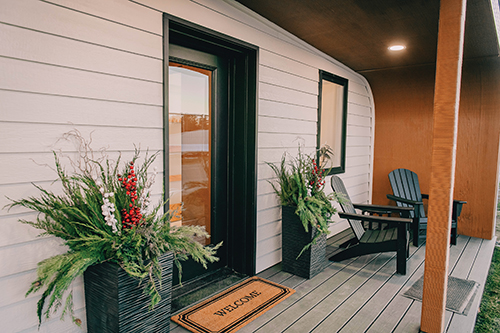
The Material
The house was completed in November 2022, but the material it’s made from draws on decades of industry experience, during which researchers learned how to mix different materials and extrude them into building products. The most familiar products are made with a blend of wood fibers and thermoplastic resins — outdoor decking, for example.
But while the BioHome builds on that industry experience, Dagher says that the material isn’t the same as that that used for decking. The big difference is that there are no plastics. “Rather than wood fibers mixed with petroleum-based or recycled plastic, the material is 100% bio-based, using wood fibers plus bio-based resin,” he says. “Also, the material’s chemistry has been modified to optimize it for 3D printing.”
The wood fibers are from “residuals” — waste wood from sawmills, which doesn’t make the grade for construction lumber. Dagher says that about a million tons of wood residuals are generated in Maine alone each year. In the past, those residuals typically went to pulp and paper mills, but with the closure of seven Maine mills over the last few years, there’s an abundance of residuals available.
In the first step of the process, “wood residuals are dried and ground up into what looks like whole wheat flour,” he explains. This wood flour is mixed with an equal weight of a bio-based resin. “Essentially, you take the sugars out of the biomaterials and use it to produce the resin. We combine the flour and resin through a heating and mixing process,” Dagher says. The resin bonds the wood fibers together.
The material is made into small pellets with a diameter of less than 0.2 inches. When it’s time to print, the pellets are put into an extruder head. They’re heated and melted to the consistency of, as Dagher describes it, “hot toothpaste.”
As is usual with 3D printing, the material is put down in layers. At ordinary room temperature, it cools and hardens quickly enough that another layer can be printed on top of the previous one after two to five minutes. “If we go around the perimeter [of the home], by the time we come back to the beginning, we’re usually able to put another layer over the top,” Dagher says. The finished pieces are solid enough to be moved within a few minutes, but they’re still hot, so it’s easier to let them cool for a bit longer.
To print the one-bedroom, one-bathroom, 600 sq. ft. BioHome, 20 tons (40,000 pounds) of material was needed for the floors, walls and roof.
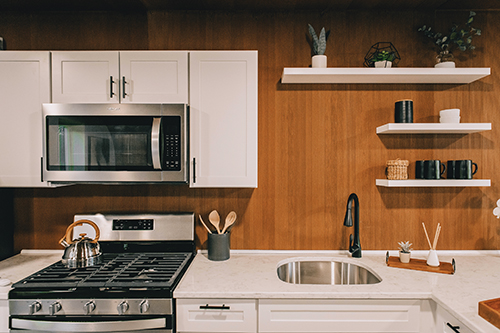
The Printing Process
“We did it this way so we could transport it by road to the site,” Dagher explains.
All the printed modules were six-sided (enclosed on all sides). That meant the team could finish them before delivering them — installing drywall, painting, putting in the kitchen, plumbing, electrical, and so forth, just as with a standard modular home. “When we got it to the site, we just had to bolt the modules together,” Dagher says.
Most homes that are 3D-printed with concrete use wood trusses for the roof. However, the BioHome’s roof trusses could be 3D-printed because the material has less than half the density of concrete. “Concrete weighs near 150 pounds per sq. ft., whereas this material is 60 to 70 pounds per sq. ft.”
When the lab first started printing, their throughput was only 20 pounds an hour, but they eventually ramped that up to 120 pounds an hour. “Recently, we designed some equipment with partners, so we can do 500 pounds an hour and our goal is 1000 pounds an hour,” Dagher says. “If we can print [a house this size] at 500 pounds per hour, it would take 80 hours. If we can print at 1000 pounds an hour, we could print it in 40 hours,” Dagher says.
He believes that, at 1000 pounds per hour, costs can be competitive with existing building methods.
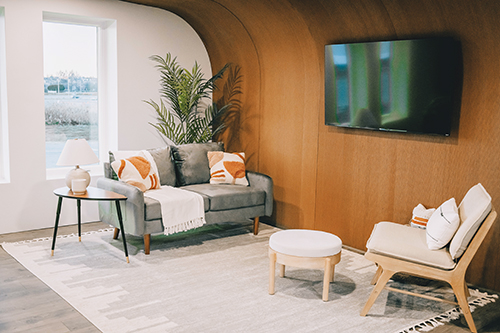
Finishing Touches
Composite siding was added to the front of the home, but only to show that it’s possible. Additional siding isn’t really needed — the material can stay exposed to the elements.
For the same reason, the team also hung drywall — which isn’t necessary — on some of the interior walls. “It’s very easy to put drywall on if you want to. You just screw vertical wood furring strips onto the wall with a screw gun, and then attach the drywall to those strips,” Dagher explains.
Cabinets and other fixtures can also be attached directly to the composite material. According to Dagher “there’s no need to find studs because the entire wall is strong enough to support cabinets, which gives you a lot of flexibility in the layout of the home.”
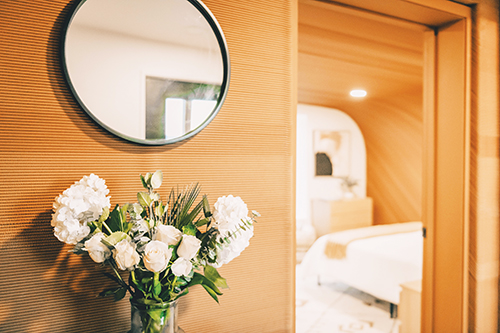
More Efficient, Less Wasteful
The research team measured the energy needed to produce the wood flour, the bio-resin, make the pellets, etc. and Dagher says that, compared to stick-building, construction of the BioHome uses much less energy.
To come up with this figure, the researchers used data from academic literature that summarized 17 studies of the energy consumed during construction of North American wood-frame, stick-built houses. They compared this to the BioHome.
“The analysis showed that, up to and including the structure being installed on the foundation, the 3D-printed construction of a 600 sq. ft. home using our printer and our material uses approximately 20% less energy than that of a wood-frame, stick-built house [of the same size],” Dagher explains. Their continued research aims to understand the “energy impacts of different biomaterial formulations [i.e. the percentage of wood residuals, different types of resin, etc.] and different print conditions.”
The house also generated a lot less waste compared to a stick-built house. “For example, when stick-building, you put up the framing, then attach the plywood or OSB sheathing, and then you cut the openings for the windows and doors — and all that cut away sheathing becomes waste,” Dagher says. “We’re able to print around the windows and doors, so there’s no waste.”
The cavities in the 3D-printed roof and walls were filled with blown-in wood-based insulation, because the team wanted everything to be bio-based and renewable. “You can achieve R-values similar to even fiberglass insulation by simply scaling the thickness,” Dagher says. “That includes roof thickness. An advantage of this technology is that you’re not limited to [the sizes of commercially available] roof trusses.”
The depth of the printed roof truss used in the BioHome was about 10 inches, which provided an R-value of about 30. “We could have printed a 14- or 15-inch roof truss to maximize R-value, which would have provided an R-value of 46-50,” Dagher says.
On an independent project, the Advanced Structures & Composites Center is working with TimberHP, a Maine company that’s using a converted pulp and paper mill to make wood insulation. The blown-in insulation used in the BioHome is similar to that which is commercially available from TimberHP.
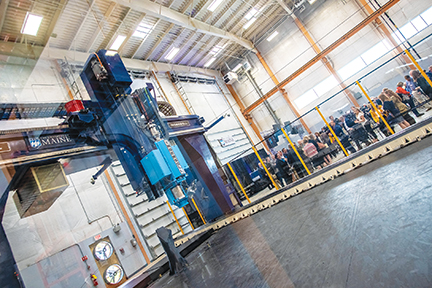
Data Collection
Various monitors were attached to the home and data collected over the year since its completion.
The indoor temperature was maintained between 65 and 70F (18 to 21 C) although the house was exposed to outdoor temperatures as low as 1F (-17C) and as high as 105F (41C). That kind of temperature difference can cause materials to expand and contract. “We were concerned, for example, about drywall cracking, but that didn’t happen.”
Dagher says the team learned a lot, though, and “there are things we’ll do differently next time to better allow for expansion and contraction of the material, such as how it attaches to the foundation.” It expands and contracts more than typical wood materials.
He says that the house was also exposed to windstorms with gusts of 70 to 80 miles per hour that took out electricity across the state, as well as snowstorms with significant accumulation of snow on the roof. The research team was happy with how the house performed.
“We’ll take what we learned in this home and implement improvements. We plan to design and print the second home this year,” Dagher says. For example, they figured out a more efficient way to 3D-print the roof trusses. The next houses the team prints will be inhabited (unlike the prototype). They will be part of a 9-home development in the greater Bangor area, for people experiencing, or at risk of, homelessness.
As well as performance, recyclability was also important to the team. “We have a graduate student right now who’s doing research on recyclability. He’s grinding up the material and printing with it again and looking at how the material properties change over every cycle. We’re looking at five re-use cycles to see how the materials change and how they could be re-used.”
Zena Ryder writes about construction and robotics for businesses, magazines, and websites. Find her at zenafreelancewriter.com. All images courtesy University of Maine, Advanced Structures & Composites Center.